Stress breaking process of automatic spring coiler for spring wires
A technology of spring steel wire and spring coiling machine is applied in the field of disconnection after the forming process of automatic spring coiling machine, which can solve the problems of linear deviation of spring force value, verticality, large closing force of spring support ring, and out-of-control spring precision, so as to avoid The effect of dimension deviation, reducing use intensity and ensuring production quality
- Summary
- Abstract
- Description
- Claims
- Application Information
AI Technical Summary
Problems solved by technology
Method used
Image
Examples
Embodiment 1
[0037] Such as figure 1 and figure 2 As shown, a spring steel wire automatic spring coiling machine stress breaking process, after the spring wire is formed by the automatic spring coiling machine, an auxiliary core 3 is set on the inner circumference of the spring, and a tool 2 located on the outer circumference of the spring is used to process a spring steel wire. At the stress concentration point 1, then the spring rotates at an angle of 90°, and the tool 2 is pressed against the spring, and the tool 5 set on the outer circumference of the spring is moved upwards, that is, an inward breaking external force is applied on the outer circumference of the spring, and the breaking external force makes the spring diameter The spring is bent and broken at the stress concentration point 1.
Embodiment 2
[0039] Such as figure 1 and image 3 As shown, a spring steel wire automatic spring coiling machine stress breaking process, after the spring wire is formed by the automatic spring coiling machine, an auxiliary core 3 is set on the inner circumference of the spring, when the tool 2 on the outer circumference of the spring processes the stress concentration point on the spring steel wire 1. The auxiliary core 3 plays a supporting role on the inner circumference of the spring to prevent the spring from being squeezed under force, and then the spring is rotated at an angle of 90°, and the modified auxiliary breaking tool 7 is used to hold the spring, and the dragging frame 5 is used to pair the outer spring The circumference exerts an inward breaking force, causing the spring to bend and break at the stress concentration point 1.
[0040] Compared with Embodiment 1, this embodiment adopts a modified auxiliary breaking tool 7 to replace the cutter 2, thereby ensuring that there i...
Embodiment 3
[0042] Such as Figure 4 and Figure 5 As shown, a spring steel wire automatic spring coiling machine stress breaking process, the spring wire is formed on the automatic spring coiling machine, to the cutting position, the core knife 4 is set on the inner circumference of the spring, the knife 2 and the core knife 4 are placed inside and outside the spring Process two indentations on the circumference and act on one stress concentration point 1, pull out the core knife 4, feed the material 180 degrees, and then clamp the breaking tool 6 on the outer circumference of the spring, and fix one end of the clamping and breaking tool 6 against the spring , the other end exerts an inward breaking external force, and the breaking external force makes the spring radially stressed, acting on the stress concentration point 1, so that the spring is bent and broken at the stress concentration point 1.
PUM
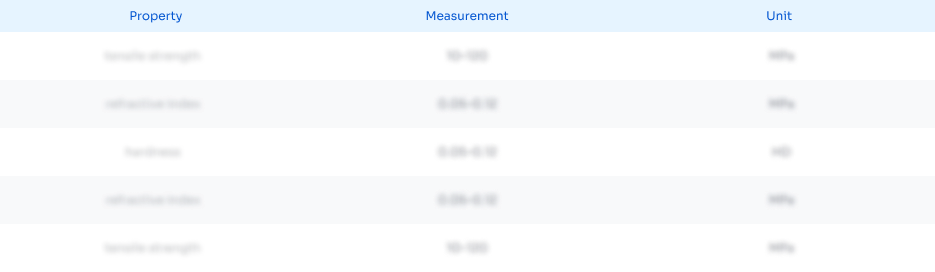
Abstract
Description
Claims
Application Information

- R&D
- Intellectual Property
- Life Sciences
- Materials
- Tech Scout
- Unparalleled Data Quality
- Higher Quality Content
- 60% Fewer Hallucinations
Browse by: Latest US Patents, China's latest patents, Technical Efficacy Thesaurus, Application Domain, Technology Topic, Popular Technical Reports.
© 2025 PatSnap. All rights reserved.Legal|Privacy policy|Modern Slavery Act Transparency Statement|Sitemap|About US| Contact US: help@patsnap.com