Detection system for high-speed wire rod steel heaping and judgment method
A detection system and high-speed wire rod technology, which is applied in the field of stacking steel detection system in rolling high-speed wire rod workshop, can solve the problems of delay in judgment, difficult processing, and very large production impact, so as to achieve the effect of accurate judgment and reduction of fault processing time.
- Summary
- Abstract
- Description
- Claims
- Application Information
AI Technical Summary
Problems solved by technology
Method used
Image
Examples
Embodiment 1
[0022] Embodiment 1: as figure 1 As shown, a detection system for stacking high-speed wire rod steel, the detection system is installed on the rolling production line of the steel rolling high-speed wire rod workshop, and the described rolling production line is divided into heating furnace area, rough rolling Mills, intermediate rolling mills, pre-finishing mills, finishing mills, reducing and sizing mills, laying heads, loose coil conveyors, coil collection stations, PF lines, weighing and unloading coils.
[0023] The detection system includes a PLC control system, a detection looper, a looper detector and an accident shear, the described looper detector is installed on the detection looper, and the described detection looper is respectively installed at the pre-roller of the rolling production line. On the finishing rolling group and the finishing rolling group, the loop detector and the accident shear are all connected to the PLC control system through lines. The number ...
Embodiment 2
[0024] Embodiment 2: as figure 1 As shown, the PLC control system of the present invention is AC800PECPLC system. The scan period of the AC800PECPLC system of the present invention is 1 ms.
Embodiment 3
[0025] Embodiment 3: as figure 1 and 2 As shown, the judgment method of the detection system of a kind of high-speed wire stack steel provided by the present invention, described judgment method comprises the following operation steps:
[0026] 1) On the PLC control system, set the limited starting quantity of the detection looper.
[0027] 2) During the working process of the system, the looper detector starts to work, check the working status of the detection looper, if the detection looper is not working normally, repeat the inspection work.
[0028] 3) After the looper detector finds that the detection looper is working normally, after a delay of 5s, it monitors the detection looper, and detects the amount of the looper every second, and 5s is a cycle; During the monitoring operation, the looper detector judges the lifting amount of the looper through the working height of the looper.
[0029] 4) When the PLC controller finds that the amount of loose sets detected excee...
PUM
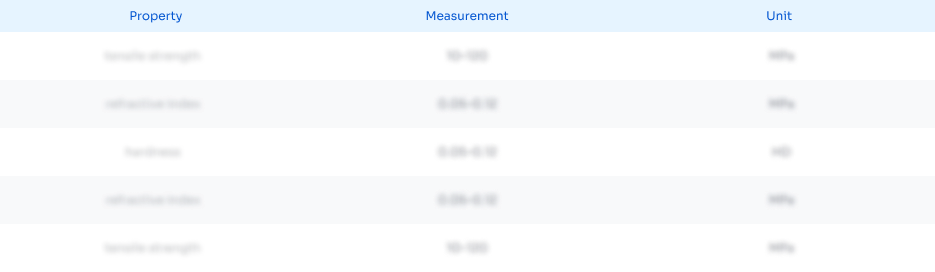
Abstract
Description
Claims
Application Information

- Generate Ideas
- Intellectual Property
- Life Sciences
- Materials
- Tech Scout
- Unparalleled Data Quality
- Higher Quality Content
- 60% Fewer Hallucinations
Browse by: Latest US Patents, China's latest patents, Technical Efficacy Thesaurus, Application Domain, Technology Topic, Popular Technical Reports.
© 2025 PatSnap. All rights reserved.Legal|Privacy policy|Modern Slavery Act Transparency Statement|Sitemap|About US| Contact US: help@patsnap.com