Drying sintering furnace and drying sintering method
A technology for sintering furnaces and sintering zones, applied in the direction of furnaces, furnace components, furnace types, etc., can solve problems such as difficulty in ensuring the temperature in the temperature zone, temperature inconsistency, etc., achieve easy implementation, prevent waste gas pollution control, and improve stability Effect
- Summary
- Abstract
- Description
- Claims
- Application Information
AI Technical Summary
Problems solved by technology
Method used
Image
Examples
Embodiment Construction
[0036] The present invention will be further described below according to the accompanying drawings and specific embodiments, but the embodiments of the present invention are not limited thereto.
[0037] like figure 1 , figure 2 , image 3 , Figure 4 and Figure 5 As shown, a drying and sintering furnace includes a conveying platform 1. The upper plane of the conveying platform 1 is provided with a conveying belt 105. The conveying belt 105 is driven by two rollers 3 controlled by a single motor for transportation. The conveying platform 1 is from the feed end to the The discharge end is provided with a silicon wafer preheating zone 4, a waste gas combustion zone 5, a sintering zone 6 and a silicon wafer cooling zone 7 in sequence, and a plurality of drying preheating furnaces 8 are arranged at intervals in the silicon wafer preheating zone 4, and a plurality of The temperature of the drying preheating furnace 8 gradually rises, the waste gas combustion zone 5 is provid...
PUM
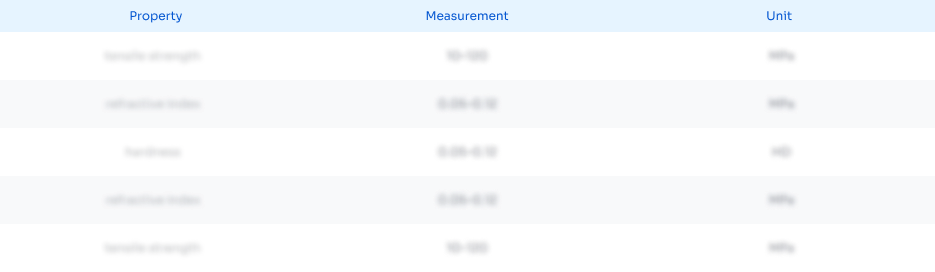
Abstract
Description
Claims
Application Information

- R&D Engineer
- R&D Manager
- IP Professional
- Industry Leading Data Capabilities
- Powerful AI technology
- Patent DNA Extraction
Browse by: Latest US Patents, China's latest patents, Technical Efficacy Thesaurus, Application Domain, Technology Topic, Popular Technical Reports.
© 2024 PatSnap. All rights reserved.Legal|Privacy policy|Modern Slavery Act Transparency Statement|Sitemap|About US| Contact US: help@patsnap.com