A Large Range Transient Current Sensor Based on Tunneling Magnetoresistance
A technology of tunneling reluctance and transient current, which is applied in the field of sensing and measurement, can solve the problems of high preparation cost, limited installation space, and consumption of metal resources, and meet the requirements of wire thickness and number of turns flexibly, and is easy to debug and install The effect of maintaining and weakening the air gap magnetic field
- Summary
- Abstract
- Description
- Claims
- Application Information
AI Technical Summary
Problems solved by technology
Method used
Image
Examples
Embodiment Construction
[0017] A large-range transient current sensor based on tunneling magnetoresistance proposed by the present invention will be further described in detail in conjunction with the accompanying drawings and specific embodiments as follows:
[0018] The large-range transient current sensor based on tunneling magnetoresistance proposed by the present invention has a structure such as figure 2 As shown, it includes: split magnetic ring 1, tunneling magnetoresistive magnetic sensor chip 2, signal conditioning circuit 3 (including instrument amplifier and power supply), analog-to-digital conversion device 4, data processing device 5 (compared with traditional tunneling magnetoresistive current The sensor device has the same composition structure); on this basis, it also includes a closed coil 6; wherein, the closed coil 6 is wound on the open magnetic ring 1 to expand the current measurement range; the tunneling at the opening of the open magnetic ring 1 The magnetoresistive magnetic ...
PUM
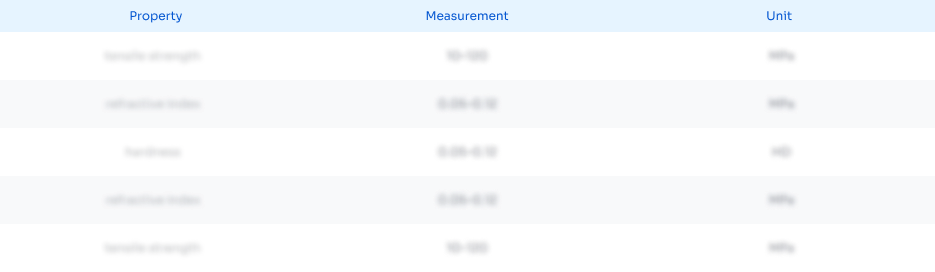
Abstract
Description
Claims
Application Information

- R&D
- Intellectual Property
- Life Sciences
- Materials
- Tech Scout
- Unparalleled Data Quality
- Higher Quality Content
- 60% Fewer Hallucinations
Browse by: Latest US Patents, China's latest patents, Technical Efficacy Thesaurus, Application Domain, Technology Topic, Popular Technical Reports.
© 2025 PatSnap. All rights reserved.Legal|Privacy policy|Modern Slavery Act Transparency Statement|Sitemap|About US| Contact US: help@patsnap.com