Saturated steam catalytic burner used for cement decomposition furnace
A technology of cement decomposition furnace and catalytic burner, which is applied in the direction of burning powder fuel burners, burners, and solid fuel combustion, etc., which can solve the problems of poor swirling effect, heat waste, and increased coal consumption, so as to reduce erosion and wear strength, suppress fuel-type NOx, and improve service life
- Summary
- Abstract
- Description
- Claims
- Application Information
AI Technical Summary
Problems solved by technology
Method used
Image
Examples
Embodiment Construction
[0026] like figure 1 and figure 2 As shown, a saturated steam catalytic combustor for a cement decomposition furnace of the present invention includes: an inner sleeve 6 , a saturated steam channel 4 , a catalyst tank 3 , a conical chamfer 8 , and a swirling air fin 10 . Wherein, the catalyst tank 3 is connected with the saturated steam channel 4, and the saturated steam channel 4 is connected with the inner sleeve 6 (the connection position between the saturated steam channel 4 and the inner sleeve 6 is located at the front section of the inner sleeve 6 at the diameter change), and the inner sleeve 6 The outlet end is provided with a conical chamfer 8 and a swirl air fin 10 . The saturated steam 1 enters the saturated steam channel 4 through the catalyst tank 3 in two ways. Catalyst tank 3 is equipped with a catalyst to promote the reaction between pulverized coal and saturated steam, and catalyst tank 3 plays a role in adjusting the resistance and flow rate of saturated s...
PUM
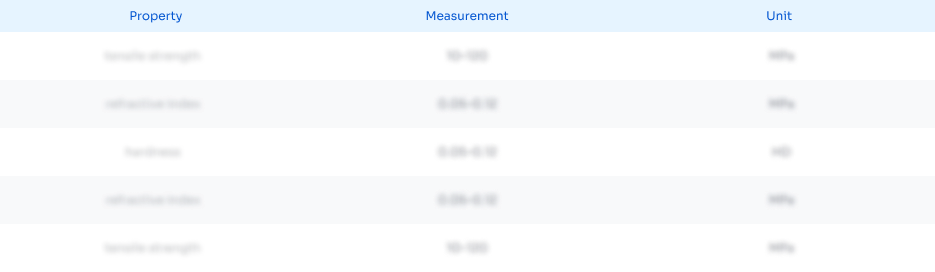
Abstract
Description
Claims
Application Information

- R&D
- Intellectual Property
- Life Sciences
- Materials
- Tech Scout
- Unparalleled Data Quality
- Higher Quality Content
- 60% Fewer Hallucinations
Browse by: Latest US Patents, China's latest patents, Technical Efficacy Thesaurus, Application Domain, Technology Topic, Popular Technical Reports.
© 2025 PatSnap. All rights reserved.Legal|Privacy policy|Modern Slavery Act Transparency Statement|Sitemap|About US| Contact US: help@patsnap.com