Alkaline electrolyte and nickel electroplating method in alkaline system
An electrolyte and electroplating nickel technology, which is applied in the field of alkaline electrolyte, can solve the problems of blackening and brittleness, blackening and brittleness of the deposited nickel layer, etc., achieve good bonding force and corrosion resistance, meet industrial needs, and have great prospects Effect
- Summary
- Abstract
- Description
- Claims
- Application Information
AI Technical Summary
Problems solved by technology
Method used
Image
Examples
Embodiment 1
[0031] Configure 250mL of electrolyte containing nickel chloride 30g / L, ammonium chloride 40g / L, ammonia water 50g / L, and sodium benzenesulfinate 0.05g / L. Use a ruthenium-titanium electrode anode, soak it in 1mol / L hydrochloric acid for 20 minutes to remove impurities attached to the surface, take it out, rinse it with deionized water, and dry it with cold air. Using stainless steel as the cathode material, after grinding with 1#, 3#, and 5# sandpaper, degreasing with absolute ethanol, washing with deionized water and drying with cold air, put the cathode and anode into the electrolytic cell at the same time, and control the electrodeposition temperature to 20℃, the current density is -100A / m 2 , Stir the electrolyte at a speed of 200r / min. After 60 minutes of electrodeposition, take out the cathode, rinse the residual electrolyte on the surface with water, and dry it with cold air to obtain a bright and smooth nickel-plated layer.
example 1
[0032] The current efficiency of nickel electroplating in Example 1 is 97.21%.
Embodiment 2
[0034] Configure 250mL of electrolyte containing nickel chloride 500g / L, ammonium chloride 400g / L, ammonia water 500g / L, and sodium benzenesulfinate 2g / L. Use ruthenium-titanium electrode anode, immerse in 5mol / L hydrochloric acid for 5 minutes to remove impurities attached to the surface, take it out, rinse it with deionized water, and dry it with cold air. Using stainless steel as the cathode material, after grinding with 1#, 3#, and 5# sandpaper, degreasing with absolute ethanol, washing with deionized water and drying with cold air, put the cathode and anode into the electrolytic cell at the same time, and control the electrodeposition temperature to 60℃, the current density is -500A / m 2 , Stir the electrolyte at a speed of 700r / min. After 3 minutes of electrodeposition, take out the cathode, rinse the residual electrolyte on the surface with water, and dry it with cold air to obtain a bright and smooth nickel-plated layer.
PUM
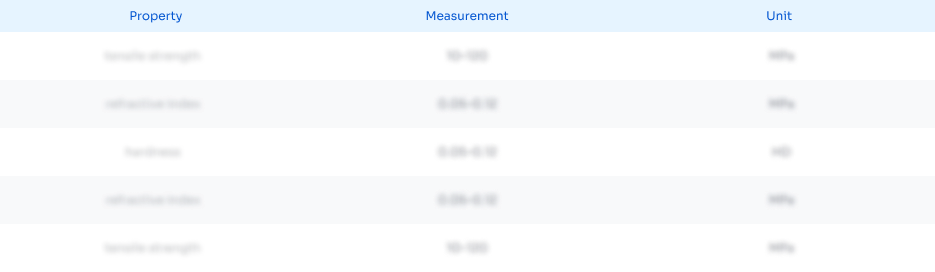
Abstract
Description
Claims
Application Information

- Generate Ideas
- Intellectual Property
- Life Sciences
- Materials
- Tech Scout
- Unparalleled Data Quality
- Higher Quality Content
- 60% Fewer Hallucinations
Browse by: Latest US Patents, China's latest patents, Technical Efficacy Thesaurus, Application Domain, Technology Topic, Popular Technical Reports.
© 2025 PatSnap. All rights reserved.Legal|Privacy policy|Modern Slavery Act Transparency Statement|Sitemap|About US| Contact US: help@patsnap.com