Dyeing technology for wood veneer/batten
A veneer and process technology, applied in the field of veneer/square dyeing process, can solve the problems of difficult promotion and application of products, poor structural stability, poor dyeing quality, etc., to ensure color consistency, strong practicability, and strong visual impact Effect
- Summary
- Abstract
- Description
- Claims
- Application Information
AI Technical Summary
Problems solved by technology
Method used
Image
Examples
Embodiment 1
[0057] This process includes the following steps:
[0058] A. Sorting: Classify the original veneer / square according to the variety, wood grain, color and tree number, and inspect and classify;
[0059] B. Blanching: Add sodium silicate, hydrogen peroxide and caustic soda in proportion to the bleaching liquid. The bleaching liquid can be reused and the interval between repeated use is 3 days. The cooking liquid is heated and the temperature of the blanching liquid is raised to 60°C, and then the sorted veneer / cubic is put into the blanching tank in batches for treatment, and blanched for 6 hours to obtain the blanched veneer / cubic;
[0060] C. Dyeing: Dyeing mixture is added to the dyeing vat, and the dyeing mixture can be reused and the interval between reuse is 3 days. The dyeing vat uses steam indirect heating to heat the dyeing mixture and raise the temperature of the dyeing mixture to 90 ℃, then put the bleached veneer / square into the dye vat, and dye for more than 8 hou...
Embodiment 2
[0069] This process includes the following steps:
[0070] A. Sorting: Classify the original veneer / square according to the variety, wood grain, color and tree number, and inspect and classify;
[0071] B. Blanching: Add sodium silicate, hydrogen peroxide and caustic soda in proportion to the bleaching liquid. The bleaching liquid can be reused and the interval between repeated use is 3 days. The cooking liquid is heated and the temperature of the blanching liquid is raised to 55°C, and then the sorted veneer / cubic is put into the blanching tank in batches for treatment, and blanched for 6 hours to obtain the blanched veneer / cubic;
[0072] C. Dyeing: the dyeing vat is added with dyeing mixture, the dyeing mixture can be reused and the interval of reuse is 3 days, the dyeing vat uses steam indirect heating to heat the dyeing mixture and raise the temperature of the dyeing mixture to 85 ℃, then put the bleached veneer / square into the dye vat, dye for more than 8 hours, and obt...
Embodiment 3
[0081] This process includes the following steps:
[0082] A. Sorting: Classify the original veneer / square according to the variety, wood grain, color and tree number, and inspect and classify;
[0083] B. Blanching: Add sodium silicate, hydrogen peroxide and caustic soda in proportion to the bleaching liquid. The bleaching liquid can be reused and the interval of repeated use is 5 days. The cooking liquid is heated and the temperature of the blanching liquid is raised to 65°C, and then the sorted veneer / cubic is put into the blanching tank in batches for treatment, and blanched for 6 hours to obtain the blanched veneer / cubic;
[0084] C. Dyeing: The dyeing vat is added with a dyeing mixture, which can be reused and the interval between reuse is 5 days. The dyeing vat uses steam indirect heating to heat the dyeing mixture and raise the temperature of the dyeing mixture to 95 ℃, then put the bleached veneer / square into the dye vat, and dye for more than 8 hours to obtain a dye...
PUM
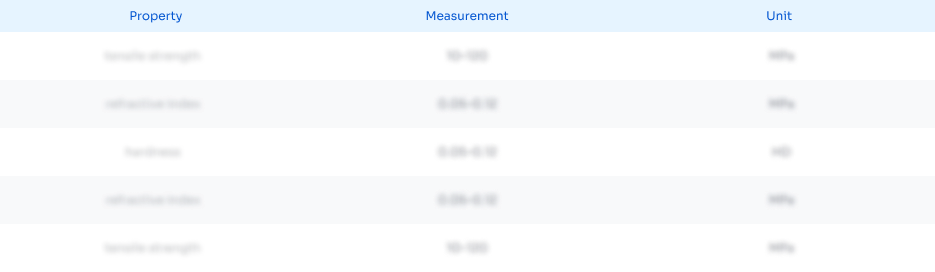
Abstract
Description
Claims
Application Information

- R&D Engineer
- R&D Manager
- IP Professional
- Industry Leading Data Capabilities
- Powerful AI technology
- Patent DNA Extraction
Browse by: Latest US Patents, China's latest patents, Technical Efficacy Thesaurus, Application Domain, Technology Topic, Popular Technical Reports.
© 2024 PatSnap. All rights reserved.Legal|Privacy policy|Modern Slavery Act Transparency Statement|Sitemap|About US| Contact US: help@patsnap.com