An Additive Manufacturing Device Based on Electron Beam Fused Filament Forming
A technology of additive manufacturing and fuse forming, which is applied in the field of additive manufacturing, can solve problems such as the inability to balance the forming surface quality and forming efficiency, the inability to realize near-net additive manufacturing of metal materials, and the rough surface of the accumulation layer, so as to improve the appearance The effects of high precision, accurate dimensions, and small machining allowances
- Summary
- Abstract
- Description
- Claims
- Application Information
AI Technical Summary
Problems solved by technology
Method used
Image
Examples
Embodiment Construction
[0017] The present invention will be described in more detail below in conjunction with the accompanying drawings and embodiments.
[0018] First of all, it should be explained that the words "thick" and "thin" mentioned in this embodiment are relative concepts, rather than a certain specific size. These words are used only to illustrate the technical solution of the present invention more clearly and clearly. , and are not intended to limit the protection scope of the present invention.
[0019] The invention discloses an additive manufacturing device based on electron beam fuse molding, which combines figure 1 and figure 2 As shown, it includes a vacuum chamber 1, a carrying platform 2, an electron gun 3, a thin wire feeding mechanism 4, a thick wire feeding mechanism 5 and a main control unit 6, wherein:
[0020] The vacuum chamber 1 is used to provide a vacuum space;
[0021] The carrying platform 2 is arranged in the vacuum chamber 1, and can translate and lift;
[0...
PUM
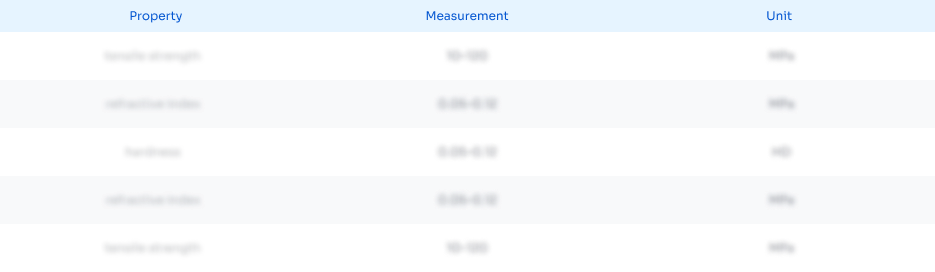
Abstract
Description
Claims
Application Information

- R&D Engineer
- R&D Manager
- IP Professional
- Industry Leading Data Capabilities
- Powerful AI technology
- Patent DNA Extraction
Browse by: Latest US Patents, China's latest patents, Technical Efficacy Thesaurus, Application Domain, Technology Topic, Popular Technical Reports.
© 2024 PatSnap. All rights reserved.Legal|Privacy policy|Modern Slavery Act Transparency Statement|Sitemap|About US| Contact US: help@patsnap.com