Preparation method of anionic acrylic acid resin retanning agent
An acrylic resin and anionic technology, which can be used in animal husbandry, chemical treatment of small raw hides/large raw hides/leather skins/furs, etc. It can solve the problems of reducing the plastic feeling of the leather body, improve the plastic feeling, and increase the filling and replenishment. Strong effect, effect of improving discoloration
- Summary
- Abstract
- Description
- Claims
- Application Information
AI Technical Summary
Problems solved by technology
Method used
Examples
preparation example Construction
[0020] The preparation method of anionic acrylic resin retanning agent, its step is as follows:
[0021] 1) Add 200-260kg deionized water and 100-150kg ethylene glycol monomethyl ether into the polymerization kettle, stir and heat to 75-80°C to obtain a mixed solution of ethylene glycol monomethyl ether and water;
[0022] 2) Add 120-180 kg of acrylic acid, 30-60 kg of methacrylic acid, 30-60 kg of methyl methacrylate, 20-30 kg of butyl acrylate and 10-30 kg of acrylonitrile into the stirred tank, and stir to obtain a mixed monomer;
[0023] 3) Dissolve 2 to 4 kg of benzoyl peroxide in 20 to 40 kg of acetone to obtain a benzoyl peroxide solution;
[0024] 4) To the mixed solution of ethylene glycol monomethyl ether and water at a temperature of 75-80°C, add the mixed monomer and benzoyl peroxide solution synchronously and uniformly for 2-3 hours, and keep warm after the addition is completed 1 to 2 hours;
[0025] 5) The temperature in the polymerization kettle is lowered to...
Embodiment 1
[0027] First, add 200 kg of deionized water and 120 kg of ethylene glycol monomethyl ether into the polymerization kettle, stir and heat to 78° C. to obtain a mixed solution of ethylene glycol monomethyl ether and water.
[0028] Add 150kg of acrylic acid, 50kg of methacrylic acid, 50kg of methyl methacrylate, 30kg of butyl acrylate and 20kg of acrylonitrile in the stirred tank, and stir to obtain a mixed monomer; get 3kg of benzoyl peroxide and dissolve it in 27kg of acetone, dissolve Completely obtain benzoyl peroxide solution.
[0029] To the mixed solution of ethylene glycol monomethyl ether and water at a temperature of 78°C, add the mixed monomer and benzoyl peroxide solution synchronously and uniformly for 2 hours, and keep warm for 2 hours after the addition; The temperature in the kettle is lowered to 40°C, the pH of the system is adjusted to 6.5 with 25% by mass of ammonia water, a certain amount of deionized water is added to the polymerization kettle, and after mix...
Embodiment 2
[0031] First, add 220kg of deionized water and 150kg of ethylene glycol monomethyl ether into the polymerization kettle, stir and heat to 79°C to obtain a mixed solution of ethylene glycol monomethyl ether and water.
[0032] Add 180kg acrylic acid, 30kg methacrylic acid, 40kg methyl methacrylate, 30kg butyl acrylate and 20kg acrylonitrile in the stirred tank again, stir to obtain mixed monomer; get 3.5kg benzoyl peroxide and dissolve in 31.5kg acetone , after the dissolution is complete, the benzoyl peroxide solution is obtained.
[0033] To the mixed solution of ethylene glycol monomethyl ether and water at a temperature of 77°C, add the mixed monomer and benzoyl peroxide solution synchronously and uniformly for 3 hours, and keep warm for 2 hours after the addition; The temperature in the kettle is lowered to 40°C, the pH of the system is adjusted to 6.5 with 25% by mass of ammonia water, a certain amount of deionized water is added to the polymerization kettle, and after mi...
PUM
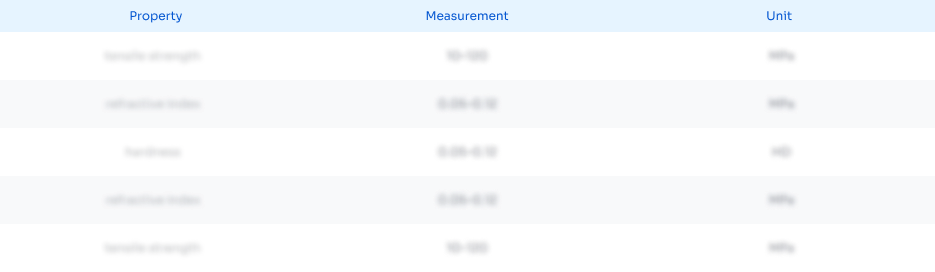
Abstract
Description
Claims
Application Information

- Generate Ideas
- Intellectual Property
- Life Sciences
- Materials
- Tech Scout
- Unparalleled Data Quality
- Higher Quality Content
- 60% Fewer Hallucinations
Browse by: Latest US Patents, China's latest patents, Technical Efficacy Thesaurus, Application Domain, Technology Topic, Popular Technical Reports.
© 2025 PatSnap. All rights reserved.Legal|Privacy policy|Modern Slavery Act Transparency Statement|Sitemap|About US| Contact US: help@patsnap.com