Preparation method of high fructose corn syrup
A fructose syrup and saccharification technology, which is applied in the production of sugar, sugar production, invert sugar production, etc., can solve the problems of lowering the monosaccharide content of saccharification liquid and affecting product quality, etc.
- Summary
- Abstract
- Description
- Claims
- Application Information
AI Technical Summary
Problems solved by technology
Method used
Image
Examples
Embodiment 1
[0020] Embodiment 1: Take F90 as an example, including the following steps:
[0021] (1) Mix starch and water in a ratio of 40:60 to make a starch emulsion with a Baume degree of 18, then add high-temperature-resistant amylase, and spray steam from a cooking machine to convert the starch emulsion into a liquefied liquid. hours, and then lower the temperature of the liquefied solution to 65°C. Put the liquefied liquid into the saccharification tank, use 15% dilute hydrochloric acid to adjust the pH to 4.4, then add glucoamylase at a ratio of 0.5g / Kg dry matter for saccharification, and use liquid chromatography to continuously detect the glucose content during saccharification. When the glucose content reaches more than 95%, stop. It has been verified that the saccharification can be completed after 48 hours; the solution is heated to 70°C to inactivate the enzyme, and then coarsely filtered with diatomaceous earth to remove impurities; successively pass through the cation exch...
Embodiment 2
[0025] Example 2: The steps of Example 2 are the same as in Example 1, except that when the recycled material is returned to the saccharification section, the mass ratio of the recycled material to the liquefied liquid is 1:10, and the dry matter content of the obtained mixed solution 2 is 32%. Use 15% dilute hydrochloric acid to adjust the pH of the mixed solution 2 to 4.5, and then add glucoamylase at a ratio of 0.5 g / Kg dry matter for saccharification. After 45 hours, a saccharification solution with a monosaccharide content of more than 95% can be obtained .
Embodiment 3
[0026] Example 3: The steps of Example 3 are the same as in Example 1, except that when the recycled material is returned to the saccharification section, the mass ratio of the recycled material to the liquefied liquid is 1:100, and the dry matter content of the obtained mixed solution 3 is 32%. Use 15% dilute hydrochloric acid to adjust the pH of the mixed solution 3 to 4.8, and then add glucoamylase at a ratio of 0.6 g / Kg dry matter for saccharification. After 48 hours, a saccharification solution with a monosaccharide content of more than 95% can be obtained .
[0027] For specific data, please refer to figure 2 and Figure 3.
[0028] Depend on figure 2 It can be seen from Figure 3 that if the recycled material is saccharified separately, even after 69 hours of saccharification, the monosaccharide content cannot reach 95%; while the liquefied solution can reach 95% after 45 hours. However, the monosaccharide content of the mixed solution 1, the mixed solution 2 and the...
PUM
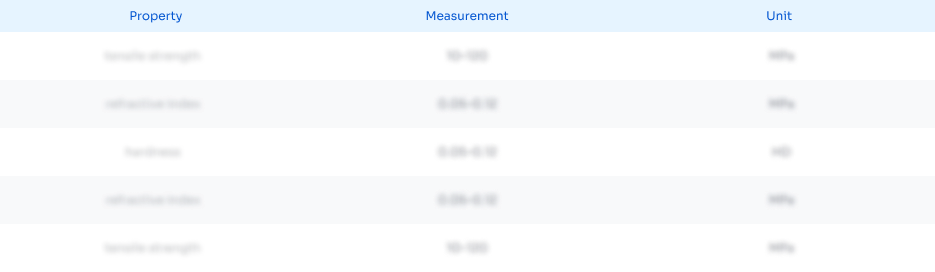
Abstract
Description
Claims
Application Information

- R&D
- Intellectual Property
- Life Sciences
- Materials
- Tech Scout
- Unparalleled Data Quality
- Higher Quality Content
- 60% Fewer Hallucinations
Browse by: Latest US Patents, China's latest patents, Technical Efficacy Thesaurus, Application Domain, Technology Topic, Popular Technical Reports.
© 2025 PatSnap. All rights reserved.Legal|Privacy policy|Modern Slavery Act Transparency Statement|Sitemap|About US| Contact US: help@patsnap.com