Vertical general assembly jig frame for container ship lashing bridge
A technology for container ships and lashing bridges, which is applied in the direction of berth, dry dock, transportation and packaging, etc., can solve the problems that cannot meet the needs of rapid, high-precision, scientific shipbuilding, difficult adjustment, deformation of lashing bridges, etc., to achieve Reduce the adjustment workload, reduce the intensity, and shorten the total group cycle
- Summary
- Abstract
- Description
- Claims
- Application Information
AI Technical Summary
Problems solved by technology
Method used
Image
Examples
Embodiment Construction
[0017] A container ship lashing bridge-vertical general group tire frame, comprising a strip tire frame 1, several frame backers and several square pipe fixing devices 2, the strip tire frame 1 is fixedly installed on the pre-embedded iron of the general group site, The several frame backers are evenly distributed on the strip tire frame 1, and the frame backers include two support rods 3 and two connecting rods 4 connecting the two support rods 3, and the lower ends of the two support rods 3 are fixedly installed on the The upper end of the strip tire frame 1, the square tube fixing device 2 is installed on the outside of two support rods 3, and the square tube fixing device 2 is used to fix the binding bridge square tube 5; There is a diagonal tie rod 6, which is located between the two connecting rods 4; the square tube fixing device 2 includes two square clips 7, the open ends of the two square clips 7 are fixedly connected, and one of the square clips The back side of 7 i...
PUM
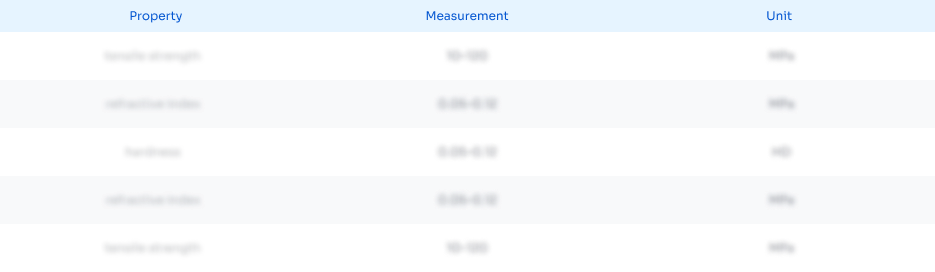
Abstract
Description
Claims
Application Information

- R&D
- Intellectual Property
- Life Sciences
- Materials
- Tech Scout
- Unparalleled Data Quality
- Higher Quality Content
- 60% Fewer Hallucinations
Browse by: Latest US Patents, China's latest patents, Technical Efficacy Thesaurus, Application Domain, Technology Topic, Popular Technical Reports.
© 2025 PatSnap. All rights reserved.Legal|Privacy policy|Modern Slavery Act Transparency Statement|Sitemap|About US| Contact US: help@patsnap.com