Improved high-temperature resistant paint
A high-temperature-resistant coating and high-temperature-resistant filler technology, which is applied in the direction of fireproof coatings, polyester coatings, polyurea/polyurethane coatings, etc., can solve the problems of poor drying at room temperature, poor adhesion and corrosion resistance of coatings, and achieve high paint film Adhesion, superior high temperature resistance, and the effect of solving solid waste problems
- Summary
- Abstract
- Description
- Claims
- Application Information
AI Technical Summary
Problems solved by technology
Method used
Image
Examples
Embodiment 1
[0053] Example 1 300°C high temperature resistant coating
[0054] Recipe one:
[0055] Select the following components in mass percentage: 8810 modified silicone resin (acrylic resin modified silicone resin) 30% (Shanghai Longxu Chemical Co., Ltd.), alkyd resin 28% (Jiangsu Champion Paint Technology Group), xylene 7.8% (Sinopec Yangzi Petrochemical Co., Ltd.), AF300 organic soil 1% (Zhejiang Shunfu Clay Chemical Co., Ltd.), carbon black 2% (Tianjin Baochi Chemical Co., Ltd.), ceramic black 1% (Shanghai Furui Chemical Co., Ltd. company), sericite powder 15% (Lingshou County Yaotai Mica Powder Factory), 1250R brand talc powder 15% (Changxing Dajing New Material Technology Co., Ltd.), silicone defoamer 0.2% (Hangzhou Zhuoli Chemical Co., Ltd. ).
[0056] Formula two (replacing the sericite powder and talcum powder of formula one with slag fine powder of the present invention):
[0057] Select the following components in mass percentage: 8810 modified silicone resin (acrylic r...
Embodiment 2
[0065] Example 2 400°C high temperature resistant coating
[0066] Recipe three:
[0067] Select the following components in mass percentage: 8810 modified silicone resin (acrylic resin modified silicone resin) 40% (Shanghai Longxu Chemical Co., Ltd.), polyurethane resin 18% (Amway Material Technology Co., Ltd.), xylene 7.8% (Sinopec Yangzi Petrochemical Co., Ltd.), AF300 organic soil 1% (Zhejiang Shunfu Clay Chemical Co., Ltd.), carbon black 2% (Tianjin Baochi Chemical Co., Ltd.), ceramic black 1% (Shanghai Furui Chemical Co., Ltd. company), sericite powder 15% (Lingshou County Yaotai Mica Powder Factory), 1250R brand talc powder 15% (Changxing Dajing New Material Technology Co., Ltd.), silicone defoamer 0.2% (Hangzhou Zhuoli Chemical Co., Ltd. ).
[0068] Formula four (replacing the sericite powder and talcum powder of formula three with the slag powder of the present invention): select the following components in mass percentage): 8810 modified silicone resin (acrylic res...
Embodiment 3
[0077] Performance tests were performed on the high-temperature-resistant coatings of formula 1 and formula 2 in Example 1, and the high-temperature-resistant coatings of formula 3 and formula 4 in Example 2, and the results are shown in Table 1 and Table 2. The result shows that the high temperature resistant coating of the present invention has superior high temperature resistance, salt resistance, alkali resistance, salt spray resistance performance compared with the high temperature resistant coating that uses traditional high temperature resistant filler such as mica powder, talcum powder, and has higher Paint film adhesion, paint film hardness.
[0078] Table 1
[0079]
[0080] Table 2
[0081]
PUM
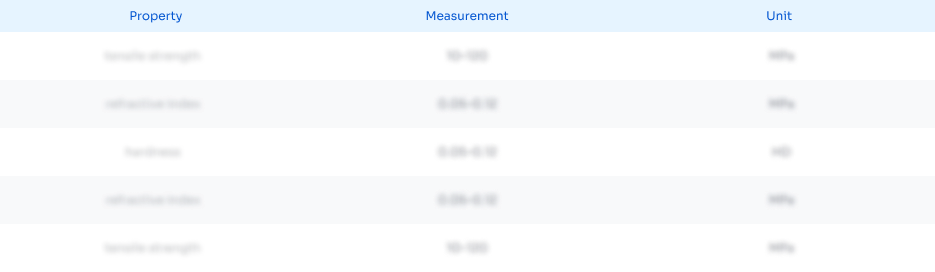
Abstract
Description
Claims
Application Information

- R&D
- Intellectual Property
- Life Sciences
- Materials
- Tech Scout
- Unparalleled Data Quality
- Higher Quality Content
- 60% Fewer Hallucinations
Browse by: Latest US Patents, China's latest patents, Technical Efficacy Thesaurus, Application Domain, Technology Topic, Popular Technical Reports.
© 2025 PatSnap. All rights reserved.Legal|Privacy policy|Modern Slavery Act Transparency Statement|Sitemap|About US| Contact US: help@patsnap.com