Anti-mud polycarboxylic acid slump retaining agent and preparation method thereof
A technology of slump retention agent and polycarboxylic acid, applied in the field of concrete admixtures, can solve the problems of high production cost and no obviousness, and achieve the effects of reducing production cost, environmental protection in the production process, and obvious anti-mud effect.
- Summary
- Abstract
- Description
- Claims
- Application Information
AI Technical Summary
Problems solved by technology
Method used
Image
Examples
example 1
[0021] Dissolve 4g of acrylic acid and 11g of hydroxyethyl acrylate in deionized water to make dripping solution A for later use, and dissolve 1.1g of chain transfer agent hypophosphite and VC0.45g of initiation aid in deionized water to make dropping solution B The material is set aside, and the initiator hydrogen peroxide (30%) 1.4g is dissolved in water to make C material and set aside. Add 155g of isopentenyl polyoxyethylene ether (TPEG) and 110g of deionized water into a 500ml container and stir to dissolve. After fully dissolving, add 3.2g of maleic anhydride and stir. After the dissolution, the dropwise addition temperature is 25- 30°C, add chain transfer agent and stir for 10 minutes, then add initiator material C and stir for 10 minutes, and at the same time, add material A and material B dropwise into the bottom liquid at a constant speed. Add material A dropwise for 2 hours, add material B dropwise for 2.5 hours, and keep warm for 1 hour; add sodium hydroxide soluti...
example 2
[0023] Dissolve 6g of acrylic acid and 15g of hydroxypropyl acrylate in deionized water to make dripping solution A for later use; dissolve 1.5g of chain transfer agent hypophosphite and VC0.6g of initiation aid in deionized water to make dropping solution B The material is set aside, and the initiator hydrogen peroxide (30%) 2.8g is dissolved in water to make C material and set aside. Add 170g of isopentenyl polyoxyethylene ether (TPEG) and 120g of deionized water into a 500ml container and stir to dissolve it. After fully dissolving, add 5.3g of maleic anhydride and stir. After the dissolution, the dropwise addition temperature is 25- 30°C, add chain transfer agent and stir for 10 minutes, then add initiator material C and stir for 10 minutes, and at the same time, add material A and material B dropwise into the bottom liquid at a constant speed. Add material A dropwise for 3 hours, add material B dropwise for 3.5 hours, and keep warm for 1 hour; add sodium hydroxide solutio...
example 3
[0025] Dissolve 4.5g of acrylic acid, 8.6g of hydroxyethyl acrylate, and 3.8g of hydroxypropyl acrylate in deionized water to prepare dropwise liquid A for later use. Dissolve 1.2g of chain transfer agent hypophosphite and 0.85g of initiation aid VC in Deionized water is prepared as material B for dropwise addition, and 3.2 g of initiator hydrogen peroxide (30%) is dissolved in water to form material C for later use. Add 165g of isopentenyl polyoxyethylene ether (TPEG) and 115g of deionized water into a 500ml container and stir to dissolve it. After fully dissolving, add 4.5g of maleic anhydride and stir. After the dissolution, the dropwise addition temperature is 25- 30°C, add chain transfer agent and stir for 10 minutes, then add initiator material C and stir for 10 minutes, and at the same time, add material A and material B dropwise into the bottom liquid at a constant speed. Add material A dropwise for 2.5 hours, add material B dropwise for 3.0 hours, and keep warm for 1....
PUM
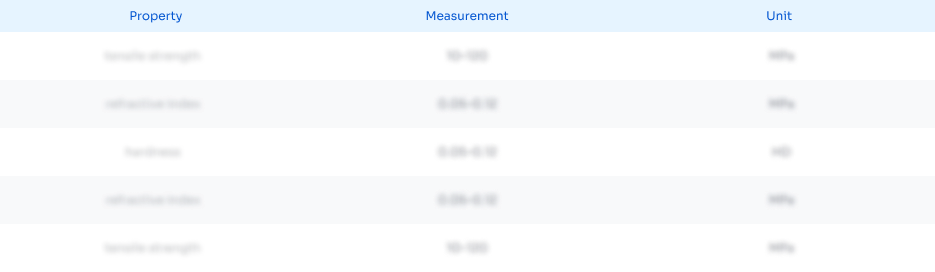
Abstract
Description
Claims
Application Information

- R&D
- Intellectual Property
- Life Sciences
- Materials
- Tech Scout
- Unparalleled Data Quality
- Higher Quality Content
- 60% Fewer Hallucinations
Browse by: Latest US Patents, China's latest patents, Technical Efficacy Thesaurus, Application Domain, Technology Topic, Popular Technical Reports.
© 2025 PatSnap. All rights reserved.Legal|Privacy policy|Modern Slavery Act Transparency Statement|Sitemap|About US| Contact US: help@patsnap.com