Hydraulic floating workpiece support
A workpiece and hydraulic technology, applied in the field of hydraulic floating workpiece support, can solve the problems of cumbersome, difficult processing and high cost, and achieve the effect of solving the operation process
- Summary
- Abstract
- Description
- Claims
- Application Information
AI Technical Summary
Problems solved by technology
Method used
Image
Examples
Embodiment 1
[0024] Such as figure 1 When the work is shown, the top surface of the top column 2 is pressed down by the gravity of the workpiece. After overcoming the supporting force of the weak spring 3 and moving down to a stable position, the hydraulic switch is turned on. The hydraulic oil enters the hydraulic oil chamber from the oil inlet 14, and the pressure transmission sealing sleeve 5 After being under pressure, its inner wall exerts pressure on the tight hoop iron block 4, so that the support spring frame 9 of the tight hoop iron block 4 squeezes the rubber strip support spring 10 to deform it, and shrinks the 3 bar-shaped iron blocks of the tight hoop iron block 4 At the same time, the seam shielding sheet 8 covers the gap between the bar-shaped iron blocks of the tight hoop iron block 4 to resist the pressure transmission sealing sleeve 5 from being squeezed by the hydraulic oil into the bar-shaped iron block of the tight hoop iron block 4 In the gap, the expansion force of t...
Embodiment 2
[0028] Such as figure 1 When the work is shown, the top surface of the top column 2 is pressed down by the gravity of the workpiece. After overcoming the supporting force of the weak spring 3 and moving down to a stable position, the hydraulic switch is turned on, and the hydraulic oil enters the hydraulic oil chamber 13 from the oil inlet 14, and the pressure transmission sealing sleeve 5. After being under pressure, its inner wall exerts pressure on the tight hoop iron block 4, so that the support spring frame 9 of the tight hoop iron block 4 extrudes the rubber strip support spring 10 to make it deformed, and the 5 bar-shaped iron blocks of the tight hoop iron block 4 are reduced. At the same time, the seam mask 8 covers the gap between the bar-shaped iron blocks of the tight hoop iron block 4 to resist the pressure transmission sealing sleeve 5 from being squeezed by the hydraulic oil into the bar-shaped iron block of the tight hoop iron block 4 In the gap between them, th...
Embodiment 3
[0030] Such as figure 1 When the work is shown, the top surface of the top column 2 is pressed down by the gravity of the workpiece. After overcoming the supporting force of the weak spring 3 and moving down to a stable position, the hydraulic switch is turned on, and the hydraulic oil enters the hydraulic oil chamber from the oil inlet 14, and the pressure transmission sealing sleeve 5 After being under pressure, its inner wall exerts pressure on the tight hoop iron block 4, so that the support spring frame 9 of the tight hoop iron block 4 squeezes the rubber strip support spring 10 to deform it, and reduces the 4 bar-shaped iron blocks of the tight hoop iron block 4 At the same time, the seam shielding piece 8 covers the gap between the bar-shaped iron blocks of the tight hoop iron block 4 to resist the pressure transmission sealing sleeve 5 from being squeezed by the hydraulic oil into the bar-shaped iron block of the tight hoop iron block 4 In the gap, the expansion force ...
PUM
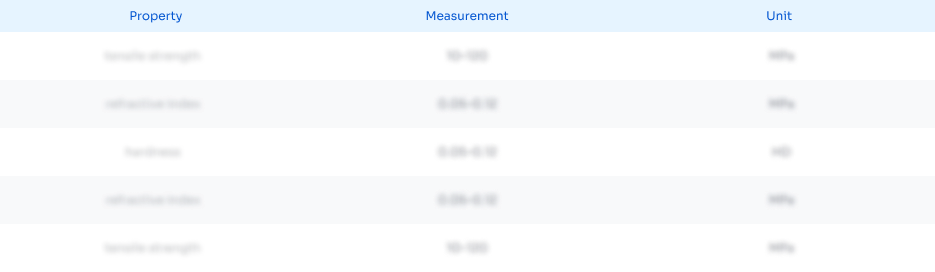
Abstract
Description
Claims
Application Information

- Generate Ideas
- Intellectual Property
- Life Sciences
- Materials
- Tech Scout
- Unparalleled Data Quality
- Higher Quality Content
- 60% Fewer Hallucinations
Browse by: Latest US Patents, China's latest patents, Technical Efficacy Thesaurus, Application Domain, Technology Topic, Popular Technical Reports.
© 2025 PatSnap. All rights reserved.Legal|Privacy policy|Modern Slavery Act Transparency Statement|Sitemap|About US| Contact US: help@patsnap.com