Vacuum coating device
A technology of vacuum coating and pulse valve, applied in the direction of gaseous chemical plating, metal material coating process, coating, etc., to solve the problem of gas concentration difference, avoid any dead angle, and improve the effect of deposition speed
- Summary
- Abstract
- Description
- Claims
- Application Information
AI Technical Summary
Problems solved by technology
Method used
Image
Examples
Embodiment 1
[0075] Figure 3A It is the first embodiment of the patent of the present invention, the gas distribution pipes 102 / 105 / 103 / 104 inside the shower plate 100; the gas distribution pipes 102 / 105 are respectively connected with the gas pipes 200 / 500 of the reaction gas; 104 is respectively connected to the gas pipe 300 / 400 of the reaction gas, and the gas inlet pipe 200 / 300 / 400 / 500 is respectively connected to the three-way pulse valve 201; one port of the three-way pulse valve is connected to the reaction gas 202, and the other port is connected to the inert gas 203 , the third port is connected with the gas inlet pipe 200 / 300 / 400 / 500.
[0076] In this embodiment, the gas inlet pipes 200 / 300 / 400 / 500 and the three-way pulse valves are symmetrically distributed, and the internal gas distribution pipes 102 / 105 / 103 / 104 of the spray plate 100 are arranged crosswise; the gas pipes are provided with two The gas inlet pipes 200 / 500 and 300 / 400, the gas inlet pipe 200 / 500 is a pipe, and ...
Embodiment 2
[0084] Such as Figure 3B As shown, the difference between the second embodiment and the first embodiment is that the intake pulse valve is composed of two two-way pulse valve groups, which include a two-way pulse valve 211 for a reactive gas and a two-way pulse valve 212 for an inert gas; The reaction gas two-way pulse valve 211 of the channel is in the normally closed state, and the reaction gas channel is opened until the end of the pulse time during the pulse; the other inert gas two-way pulse valve 212 for controlling purge can be in the normally open state, and the pulse valve group The controlled reaction gas and the inert gas meet in the external gas inlet pipe before entering the spray plate 100; when one pulse valve controlling the reaction gas channel is opened, the other pulse valves controlling the reaction gas channel are closed.
[0085] In this embodiment, the reactive gas two-way pulse valves 211 , 311 , 411 and 511 have the same structure, and the inert gas t...
Embodiment 3
[0087] Such as Figure 3C As shown, the difference between this embodiment and Embodiments 1 and 2 is that pulse valves with different functions are respectively provided at the two ports of each gas inlet pipe, one end of which is a three-way pulse valve 201, allowing reaction gas and purging The inert gas enters the reaction chamber, and the other end is the suction pulse valve 404. One end of the suction pulse valve 404 is connected to the gas inlet pipe, and the other end is connected to the gas recovery port 406. The suction pulse valve 404 allows part of the reaction gas and the inert gas for purging Suck back to the vacuum pump.
[0088] The gas flow controller 405 is placed in front of the gas inlet pipe of the described suck-back pulse valve 404, and the described suck-back pulse valve 404 can be in a normally open state, or can be in a closed state when the intake pulse valve is opened. The suction pulse valve is open when the air pulse valve is closed.
[0089] Fo...
PUM
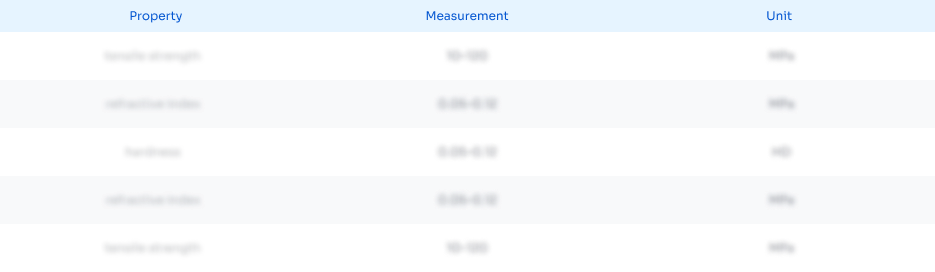
Abstract
Description
Claims
Application Information

- Generate Ideas
- Intellectual Property
- Life Sciences
- Materials
- Tech Scout
- Unparalleled Data Quality
- Higher Quality Content
- 60% Fewer Hallucinations
Browse by: Latest US Patents, China's latest patents, Technical Efficacy Thesaurus, Application Domain, Technology Topic, Popular Technical Reports.
© 2025 PatSnap. All rights reserved.Legal|Privacy policy|Modern Slavery Act Transparency Statement|Sitemap|About US| Contact US: help@patsnap.com