Inertia piezoelectric driving motor
A piezoelectric drive and inertial technology, applied in the direction of piezoelectric effect/electrostrictive or magnetostrictive motors, generators/motors, electrical components, etc., can solve the problems of piezoelectric motors such as weak tolerance and short life
- Summary
- Abstract
- Description
- Claims
- Application Information
AI Technical Summary
Problems solved by technology
Method used
Image
Examples
Embodiment Construction
[0010] Reference figure 1 with figure 2 , Including a piezoelectric vibrator 1, a mass 2, a rotating table 3, and a base 4, and is characterized in that it also includes a composite cantilever 5 formed by laminating two materials, wherein both ends of the piezoelectric vibrator 1 are fixedly connected to the The mass 2 and the rotating disc 31; the rotating table 3 includes two parts of the rotating disc 31 and the rotating shaft 32, the rotating disc 31 and the rotating shaft 32 are fixedly connected, and the axis of the rotating shaft 32 is vertical On the upper surface of the rotating disc 31; the piezoelectric vibrator 1 is composed of a piezoelectric ceramic 11 and an elastic substrate 12 bonded together, and the bonding surface of the piezoelectric ceramic 11 and the elastic substrate 12 and the rotating disc The upper surface of 31 is vertical, and the bonding surface of the piezoelectric ceramic 11 and the elastic substrate 12 exceeds the diameter of the rotating disc...
PUM
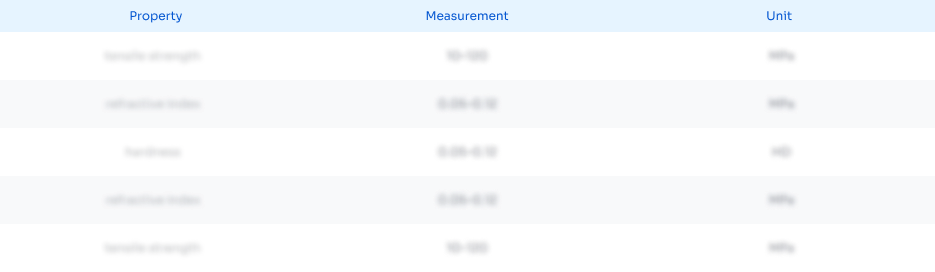
Abstract
Description
Claims
Application Information

- R&D
- Intellectual Property
- Life Sciences
- Materials
- Tech Scout
- Unparalleled Data Quality
- Higher Quality Content
- 60% Fewer Hallucinations
Browse by: Latest US Patents, China's latest patents, Technical Efficacy Thesaurus, Application Domain, Technology Topic, Popular Technical Reports.
© 2025 PatSnap. All rights reserved.Legal|Privacy policy|Modern Slavery Act Transparency Statement|Sitemap|About US| Contact US: help@patsnap.com