A metal material gradient component fusion coating forming device and method
A fusion coating and metal material technology, applied in the field of materials, can solve the problems of insufficient density of formed parts, uneven distribution of materials, and insufficient bonding force between layers of functionally graded materials, so as to shorten the forming time, improve the forming quality, and develop low cost effect
- Summary
- Abstract
- Description
- Claims
- Application Information
AI Technical Summary
Problems solved by technology
Method used
Image
Examples
Embodiment Construction
[0034] The present invention will be described in further detail below in conjunction with the accompanying drawings:
[0035] Such as Figure 1-3 Shown: The present invention patent discloses a metal material gradient structure melting coating forming device, including at least two metal melting units, namely melting unit A and melting unit B; it also includes a pneumatic drive device, a melting coating head, and a laser surface assist Remelting device and powder feeder, three-dimensional forming platform, atmosphere protection device. The pneumatic drive device is connected to the metal melting unit through a pipeline; the melting coating head is connected to the lower end of the metal melting unit, and the three-dimensional forming platform is arranged below the melting coating head; the laser surface auxiliary remelting device is arranged at the bottom of the three-dimensional forming platform On one side, the powder feeder is set on the other side of the three-dimensional f...
PUM
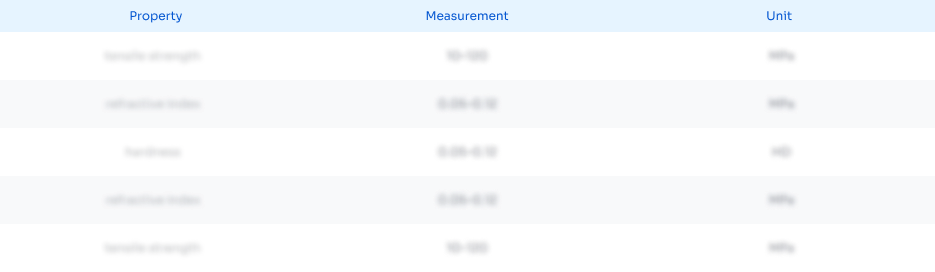
Abstract
Description
Claims
Application Information

- R&D
- Intellectual Property
- Life Sciences
- Materials
- Tech Scout
- Unparalleled Data Quality
- Higher Quality Content
- 60% Fewer Hallucinations
Browse by: Latest US Patents, China's latest patents, Technical Efficacy Thesaurus, Application Domain, Technology Topic, Popular Technical Reports.
© 2025 PatSnap. All rights reserved.Legal|Privacy policy|Modern Slavery Act Transparency Statement|Sitemap|About US| Contact US: help@patsnap.com