Low NOx burning method and low NOx burning system
A technology of combustion method and combustion system, which is applied in the field of low NOx combustion method and low NOx combustion system, and can solve the problems affecting the universality, no source of ultra-fine coal powder, increased carbon content of flue gas fly ash, etc., and achieve high NOx The effect of emission reduction rate
- Summary
- Abstract
- Description
- Claims
- Application Information
AI Technical Summary
Problems solved by technology
Method used
Image
Examples
no. 1 example
[0042] figure 1 It is a schematic diagram of the arrangement structure of the low NOx combustion system of the first embodiment of the present invention. The low NOx combustion system of the first embodiment includes a furnace body, a plasma reactor 21, a gas-solid separator 31, a reburning burner 41, a residual carbon burner 51, a pulverized coal burner 61, an overfired air nozzle 71 and a pre-combustion Exhaust the wind spout 72. Wherein, the space inside the furnace body forms a furnace 91 . The furnace 91 has a central axis 81 of the furnace, and the central axis 81 of the furnace is arranged vertically.
[0043] Reburning burner 41 , residual carbon burner 51 , pulverized coal burner 61 , pre-burned-out air spout 72 and burn-out air spout 71 are all installed on the body of heater and lead in the furnace 91 .
[0044] In the first embodiment, the pulverized coal burner 61 is divided into two layers: the lower pulverized coal burner and the upper pulverized coal burner;...
no. 2 example
[0086] figure 2 It is a schematic diagram of the arrangement structure of the low NOx combustion system of the second embodiment of the present invention.
[0087] Such as figure 2 As shown, the low NOx combustion system of the second embodiment includes a furnace body, a plasma reactor 21, a gas-solid separator 31, a reburning burner 41, a residual carbon burner 51, a pulverized coal burner 61 and an overfired air nozzle 71 . Wherein, the space inside the furnace body forms a furnace 91 . Reburning burner 41, residual carbon burner 51, pulverized coal burner 61, burn-off air spout 71 are all installed on the body of heater and lead in the hearth 91. The furnace chamber 91 has a furnace center axis 81 and the plasma reactor 21 has a reactor center axis 11 .
[0088] In the second embodiment, the pulverized coal burner 61 is divided into two layers: the lower pulverized coal burner and the upper pulverized coal burner; the residual carbon burner 51 is arranged on one laye...
no. 3 example
[0096] image 3 It is a schematic diagram of the arrangement structure of the low NOx combustion system of the third embodiment of the present invention.
[0097] Such as image 3 As shown, the low NOx combustion system of the third embodiment includes a furnace body, a plasma reactor 21 , a reburning burner 41 , a pulverized coal burner 61 , a pre-overfired air nozzle 72 and an overfired air nozzle 71 . Wherein, the space inside the furnace body forms a furnace 91 . The reburning burner 41, the pulverized coal burner 61, the pre-burned-off air spout 72 and the over-burned air spout 71 are all installed on the body of heater and lead into the furnace 91. The furnace chamber 91 has a furnace center axis 81 and the plasma reactor 21 has a reactor center axis 11 .
[0098] In the third embodiment, the pulverized coal burner 61 is divided into three layers: the lower layer of pulverized coal burner, the middle layer and the upper layer of pulverized coal burner; the reburning b...
PUM
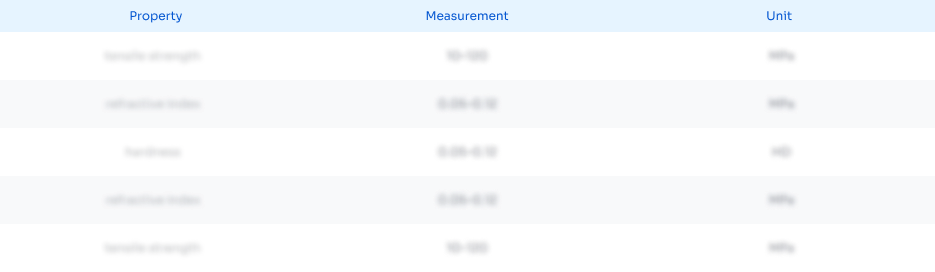
Abstract
Description
Claims
Application Information

- R&D Engineer
- R&D Manager
- IP Professional
- Industry Leading Data Capabilities
- Powerful AI technology
- Patent DNA Extraction
Browse by: Latest US Patents, China's latest patents, Technical Efficacy Thesaurus, Application Domain, Technology Topic, Popular Technical Reports.
© 2024 PatSnap. All rights reserved.Legal|Privacy policy|Modern Slavery Act Transparency Statement|Sitemap|About US| Contact US: help@patsnap.com