Self-heat-insulation wall body system of prefabricated assembling type wallboard component
A prefabricated, self-insulating technology, applied in thermal insulation, building components, walls, etc., can solve the problems of loss of energy-saving thermal insulation function, strong implementation technology, and environmental pollution.
- Summary
- Abstract
- Description
- Claims
- Application Information
AI Technical Summary
Problems solved by technology
Method used
Image
Examples
Embodiment Construction
[0023] The invention will be further described below in conjunction with the accompanying drawings.
[0024] figure 1 It is a plan view of a self-insulating wall system of a prefabricated assembled wall panel member of the present invention. When the present invention is implemented, the prefabricated assembled wall panel member 2 produced in the factory assembly line is hoisted to the pouring site of the frame column 3, and the prefabricated assembled wall panel member 2 is lifted to the casting site of the frame column 3, and the prefabricated assembled wall panel member The partial members 2 of the type wall panel member 2 and the exposed rib steel bars 58 are embedded in the column mold for on-site casting. When the columns and beams are shaped steel structures, the exposed rib steel bars are directly welded to the shaped steel columns and shaped steel beams; the prefabricated assembled wall panel member 2 can be designed as a horizontal slab in the best state or as a vert...
PUM
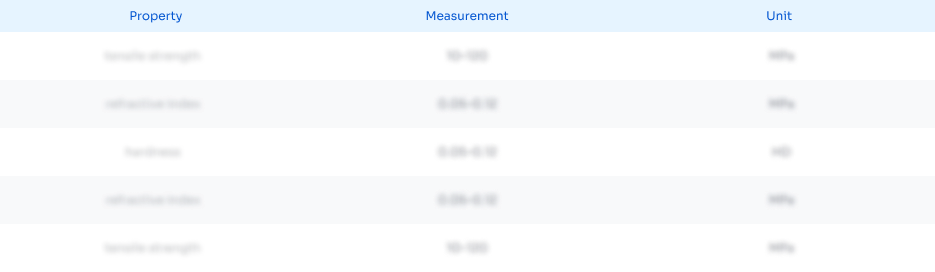
Abstract
Description
Claims
Application Information

- Generate Ideas
- Intellectual Property
- Life Sciences
- Materials
- Tech Scout
- Unparalleled Data Quality
- Higher Quality Content
- 60% Fewer Hallucinations
Browse by: Latest US Patents, China's latest patents, Technical Efficacy Thesaurus, Application Domain, Technology Topic, Popular Technical Reports.
© 2025 PatSnap. All rights reserved.Legal|Privacy policy|Modern Slavery Act Transparency Statement|Sitemap|About US| Contact US: help@patsnap.com