Corrosion-resistant cement clinker warehouse top conveyor
A clinker silo and top conveying technology, which is applied in the field of conveyors, can solve the problems of the mechanical strength of the cement clinker silo top conveyor plummeting, corrosion, and the collapse of the cement clinker silo top conveyor.
- Summary
- Abstract
- Description
- Claims
- Application Information
AI Technical Summary
Problems solved by technology
Method used
Examples
Embodiment 1
[0030] 1) Mix high manganese steel, zinc oxide, chromium oxide, nickel sulfate, graphite, asbestos, chalcocite, stibnite and cassiterite according to the weight of 100:28:10:49:6:16:18:65:38 After mixing, the raw materials were heated from 25°C to 1445°C over 25 minutes and kept for 2.5 hours, then cooled to 1400°C over 20 minutes and kept for 2.5 hours, and finally raised to 1425°C over 45 minutes and kept for 1.2 hours to obtain a melt;
[0031] 2) Mix the melt, silicon carbide, magnesium borate whiskers (4um in diameter, 100um in length) and graphene at a weight ratio of 100:35:9:11 and reheat at 1590°C for 4h, then heat at 1280°C Water quenching at ℃ for 4 min to prepare the steel material A1 in the top conveyor of the corrosion-resistant cement clinker silo.
Embodiment 2
[0033] 1) Mix high manganese steel, zinc oxide, chromium oxide, nickel sulfate, graphite, asbestos, chalcocite, stibnite and cassiterite according to the weight of 100:25:7:45:4:12:15:60:34 After mixing, the raw material is heated from 15°C to 1440°C for 20 minutes and kept for 2 hours, then cooled to 1390°C for 15 minutes and kept for 2 hours, and finally raised to 1420°C for 40 minutes and kept for 1 hour to obtain a melt;
[0034] 2) Mix the melt, silicon carbide, magnesium borate whiskers (1um in diameter, 30um in length) and graphene at a weight ratio of 100:30:8:9 and heat for a second time at 1550°C for 3h, then heat at 1240°C ℃ water quenching for 3 minutes to prepare the steel material A2 in the top conveyor of the corrosion-resistant cement clinker silo.
Embodiment 3
[0036] 1) Mix high manganese steel, zinc oxide, chromium oxide, nickel sulfate, graphite, asbestos, chalcocite, stibnite and cassiterite according to the weight of 100:31:14:52:8:18:22:71:52 After mixing, the raw materials were heated from 30°C to 1450°C for 30 minutes and kept for 3 hours, then cooled to 1410°C for 25 minutes and kept for 3 hours, and finally raised to 1430°C for 50 minutes and kept for 1.5 hours to obtain a melt;
[0037] 2) Mix the melt, silicon carbide, magnesium borate whiskers (8um in diameter, 200um in length) and graphene at a weight ratio of 100:44:10:13 and reheat at 1620°C for 5h, then heat at 1310°C °C for 5 min in water to prepare steel A3 for the corrosion-resistant cement clinker silo top conveyor.
PUM
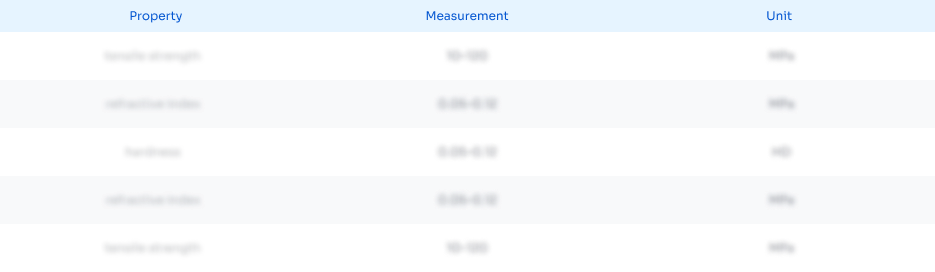
Abstract
Description
Claims
Application Information

- Generate Ideas
- Intellectual Property
- Life Sciences
- Materials
- Tech Scout
- Unparalleled Data Quality
- Higher Quality Content
- 60% Fewer Hallucinations
Browse by: Latest US Patents, China's latest patents, Technical Efficacy Thesaurus, Application Domain, Technology Topic, Popular Technical Reports.
© 2025 PatSnap. All rights reserved.Legal|Privacy policy|Modern Slavery Act Transparency Statement|Sitemap|About US| Contact US: help@patsnap.com