Magnesium light-weight refractory material and preparation method thereof
A refractory material and lightweight technology, applied in the field of refractory material production, can solve the problems of low thermal conductivity, high corrosion resistance, etc., achieve high strength and high temperature performance, and a wide range of adjustable product performance
- Summary
- Abstract
- Description
- Claims
- Application Information
AI Technical Summary
Problems solved by technology
Method used
Image
Examples
Embodiment 1
[0031] Mix 180 mesh fused magnesia fine powder and 180 mesh graphite fine powder evenly according to the molar ratio of MgO and C 3:1. The fused magnesia particles of 1-3 mm and 0.1-1 mm are used as coarse particles and medium particles respectively. Magnesia fine powder and graphite fine powder are used as the matrix part, and the ratio of coarse particles: medium particles: fine powder is 40:20:40. Use phenolic resin ethylene glycol solution as a binder, and the addition amount is 8% of the total weight of the ingredients. The mixing in the ingredients is to add the aggregate part and mix for 5 minutes, then add the phenolic resin ethylene glycol dilution and mix for 5 minutes, and then add For the fine powder part, mix for 20 minutes, and place the mixed material in an airtight container or plastic bag for 2 hours; after being trapped, the material is molded on a hydraulic press with a semi-dry method, and the molding pressure is 150 MPa. The formed sample is naturally cool...
Embodiment 2
[0035]Mix 180 mesh fused magnesia fine powder and 180 mesh graphite fine powder evenly according to the molar ratio of MgO and C 3:1. The 1-3mm and 0.1-1mm lightweight magnesia particles are respectively used as coarse particles and medium particles. Magnesia fine powder and graphite fine powder are used as the matrix part, and the ratio of coarse particles: medium particles: fine powder is 40:20:40. Use phenolic resin ethylene glycol solution as a binder, and the addition amount is 8% of the total weight of the ingredients. The mixing in the ingredients is to add the aggregate part and mix for 3 minutes, then add the phenolic resin ethylene glycol dilution and mix for 5 minutes, and then add For the fine powder part, mix for 20 minutes, and place the mixed material in an airtight container or a plastic bag for 6 hours; the material after being trapped is molded on a hydraulic press with a semi-dry method, and the molding pressure is 150MPa. Cool for half a day to 1 day, then...
Embodiment 3
[0039] Mix 180 mesh fused magnesia fine powder and 180 mesh graphite fine powder evenly according to the molar ratio of MgO and C 4:1. The 1-3mm and 0.1-1mm lightweight magnesia particles are respectively used as coarse particles and medium particles. Magnesia fine powder and graphite fine powder are used as the matrix part, and the ratio of coarse particles: medium particles: fine powder is 40:20:40. With the phenolic resin ethylene glycol solution as the binding agent, the addition amount is 8% of the total weight of the batching. The mixing in the batching is to add the aggregate part and mix for 5 minutes, then add the phenolic resin ethylene glycol dilution and mix for 5 minutes, and then Add the fine powder part, mix for 20 minutes, put the mixed material in an airtight container or a plastic bag and trap it for 2 hours; the trapped material is molded on a hydraulic press with a semi-dry method, the molding pressure is 150MPa, and the formed sample Naturally cool for ha...
PUM
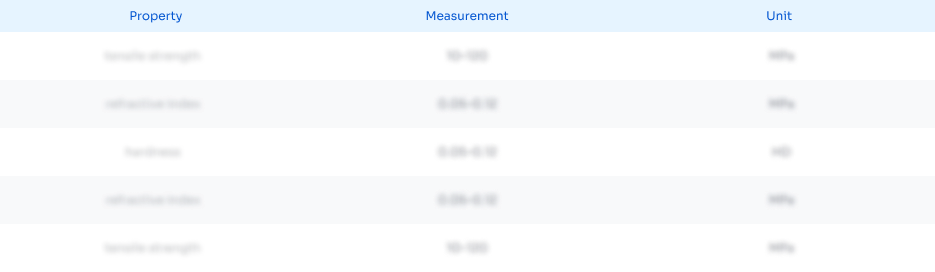
Abstract
Description
Claims
Application Information

- R&D Engineer
- R&D Manager
- IP Professional
- Industry Leading Data Capabilities
- Powerful AI technology
- Patent DNA Extraction
Browse by: Latest US Patents, China's latest patents, Technical Efficacy Thesaurus, Application Domain, Technology Topic, Popular Technical Reports.
© 2024 PatSnap. All rights reserved.Legal|Privacy policy|Modern Slavery Act Transparency Statement|Sitemap|About US| Contact US: help@patsnap.com