Bionic grabbing manipulator
A technology for grasping manipulators and manipulators, applied in the direction of manipulators, chucks, manufacturing tools, etc., can solve the problems of high control difficulty and inability to adapt to grasping of various objects, and achieve simple transmission structure, reduce control difficulty, and transmission precise effect
- Summary
- Abstract
- Description
- Claims
- Application Information
AI Technical Summary
Problems solved by technology
Method used
Image
Examples
Embodiment 1
[0020] Embodiment 1: as Figure 1-8 As shown, a bionic grasping manipulator includes manipulator index finger 1, manipulator middle finger 2, manipulator ring finger 3, manipulator little finger 4, gear shaft I5, palm support plate III6, palm support plate IV7, outer support frame 8, palm support plate II9 , Inner support frame 10, palm support plate Ⅰ11, manipulator thumb 12, gear shaft Ⅱ13, index finger control cam 14, thumb control cam 15, limit block Ⅰ16, middle finger control cam 17, large cylindrical gear 18, little finger control cam 19, ring finger Control cam 20, limit block II 21, small cylindrical gear 22, large bevel gear 23, input shaft 24, small bevel gear 25, swing rod 26, limit block III 27, limit block IV 28, finger fixing shaft 29, palm support plate Ⅳ installation position 30, little finger installation position 31, palm support plate Ⅲ installation position 32, ring finger installation position 33, middle finger installation position 34, palm support plate ...
Embodiment 2
[0023] Embodiment 2: as Figure 1-8 As shown, a bionic grasping manipulator includes manipulator index finger 1, manipulator middle finger 2, manipulator ring finger 3, manipulator little finger 4, gear shaft I5, palm support plate III6, palm support plate IV7, outer support frame 8, palm support plate II9 , Inner support frame 10, palm support plate Ⅰ11, manipulator thumb 12, gear shaft Ⅱ13, index finger control cam 14, thumb control cam 15, limit block Ⅰ16, middle finger control cam 17, large cylindrical gear 18, little finger control cam 19, ring finger Control cam 20, limit block II 21, small cylindrical gear 22, large bevel gear 23, input shaft 24, small bevel gear 25, swing rod 26, limit block III 27, limit block IV 28, finger fixing shaft 29, palm support plate Ⅳ installation position 30, little finger installation position 31, palm support plate Ⅲ installation position 32, ring finger installation position 33, middle finger installation position 34, palm support plate ...
PUM
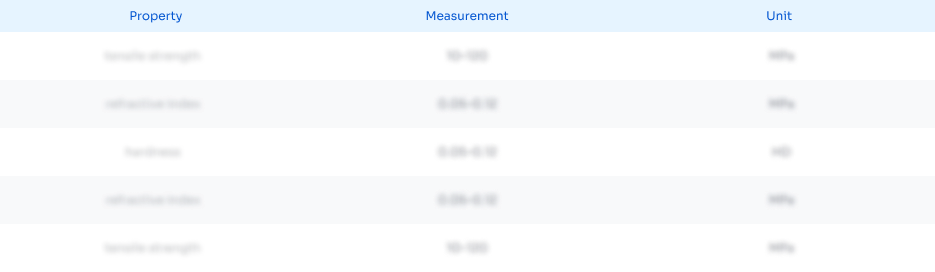
Abstract
Description
Claims
Application Information

- Generate Ideas
- Intellectual Property
- Life Sciences
- Materials
- Tech Scout
- Unparalleled Data Quality
- Higher Quality Content
- 60% Fewer Hallucinations
Browse by: Latest US Patents, China's latest patents, Technical Efficacy Thesaurus, Application Domain, Technology Topic, Popular Technical Reports.
© 2025 PatSnap. All rights reserved.Legal|Privacy policy|Modern Slavery Act Transparency Statement|Sitemap|About US| Contact US: help@patsnap.com