Mixed diamine monomer adopted chlorine-resistant nanofiltration membrane and preparation method therefor
A diamine monomer, nanofiltration membrane technology, applied in chemical instruments and methods, membrane technology, semi-permeable membrane separation, etc., can solve problems such as unsatisfactory nanofiltration membrane flux, achieve good industrial application prospects, reduce production Cost and effect of reducing usage
- Summary
- Abstract
- Description
- Claims
- Application Information
AI Technical Summary
Problems solved by technology
Method used
Image
Examples
Embodiment 1~4
[0048] Preparation of mixed diamine monomer chlorine-resistant nanofiltration membrane:
[0049] A polysulfone flat ultrafiltration membrane with a molecular weight cut-off of 70,000 was selected as the bottom membrane. The bottom membrane was immersed in the aqueous phase solution containing mixed monomers for 5 minutes, and then the solution was removed. The membrane was purged with gas or dried naturally. After the surface is dry, immerse in the organic phase solution for 5 seconds, 10 seconds, 15 seconds and 30 seconds to carry out the interfacial polymerization reaction, then remove the organic solution on the surface of the film, and place the interfacially polymerized film in the air for 1 minute, then Put it into an oven at 80° C. for heat treatment for 5 minutes. After the heat treatment, the membrane was taken out, and then rinsed with deionized water for 5 minutes to prepare a nanofiltration membrane.
[0050] The content of 2,2'-bis(1-hydroxyl-1-trifluoromethyl-2,...
Embodiment 5~8
[0056] Basically the same as in Example 3, 2,2'-bis(1-hydroxyl-1-trifluoromethyl-2,2,2,-trifluoroethyl)-4,4'- The ratio of methylene dianiline and piperazine was adjusted, and the effect of piperazine content in the mixed monomer on the performance of nanofiltration membrane was investigated.
[0057] The mixed monomer nanofiltration membranes prepared in Examples 5-8 were tested for water flux and salt interception performance, and the test results are as follows.
[0058]
Embodiment 9~12
[0060] It is basically the same as in Example 3, 5-8, but it is not necessary to rinse the prepared nanofiltration membrane, and directly immerse the nanofiltration membrane obtained after heat treatment as a whole in 3000ppm effective sodium hypochlorite solution for oxidation treatment for 1 hour, then take it out, use Ionized water for rinsing.
[0061] The mixed monomer nanofiltration membranes prepared in Examples 9-12 were tested for water flux and salt interception performance, and the test results are as follows.
[0062]
PUM
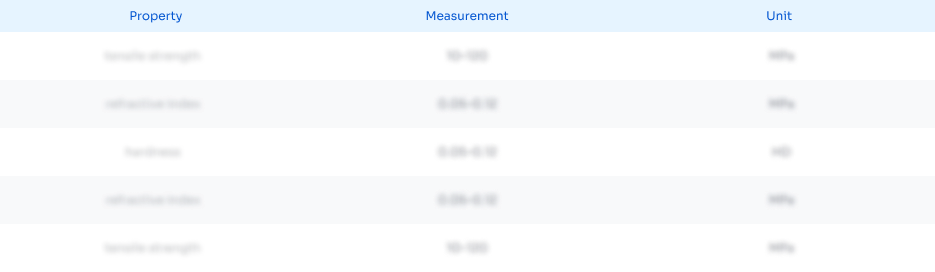
Abstract
Description
Claims
Application Information

- R&D
- Intellectual Property
- Life Sciences
- Materials
- Tech Scout
- Unparalleled Data Quality
- Higher Quality Content
- 60% Fewer Hallucinations
Browse by: Latest US Patents, China's latest patents, Technical Efficacy Thesaurus, Application Domain, Technology Topic, Popular Technical Reports.
© 2025 PatSnap. All rights reserved.Legal|Privacy policy|Modern Slavery Act Transparency Statement|Sitemap|About US| Contact US: help@patsnap.com