A semi-hollow pin plastic forming method
A plastic forming and semi-hollow technology, applied in forging/pressing/hammer devices, forging/pressing/hammering machinery, manufacturing tools, etc., can solve the problems of small range of processing materials, products with burrs, and affecting product quality. Achieve the effect of material saving, simple process and excellent smooth quality
- Summary
- Abstract
- Description
- Claims
- Application Information
AI Technical Summary
Problems solved by technology
Method used
Image
Examples
Embodiment Construction
[0034] The present invention will be further described in detail below in conjunction with the accompanying drawings and embodiments.
[0035] Such as Figure 1-12 As shown, the plastic forming method of the semi-hollow shaft pin in this embodiment is carried out according to the following steps:
[0036] Step 1: Squeeze the part blank into the bottom mold through the first stamping die 1, so that the bottom of the blank is rounded and shaped to obtain the required dimensions for the tapered hole at the tail and the upsetting of the rod;
[0037] Step 2, extruding the part 2 after step 1 through the second stamping die 3, obtaining the pre-formed hole of the head, reducing the diameter and chamfering, and upsetting the rod and head to reach the required size;
[0038]Step 3: Back-extrude the head of the part 2 after step 2 to extract holes through the third stamping die 4 to obtain the required size of the hollow hole depth of the head, and further upsetting the head and the ...
PUM
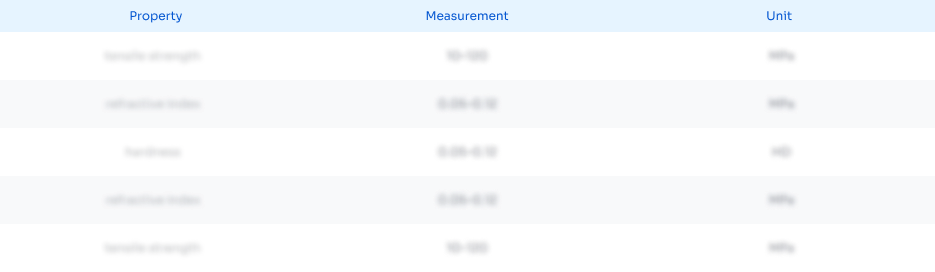
Abstract
Description
Claims
Application Information

- R&D
- Intellectual Property
- Life Sciences
- Materials
- Tech Scout
- Unparalleled Data Quality
- Higher Quality Content
- 60% Fewer Hallucinations
Browse by: Latest US Patents, China's latest patents, Technical Efficacy Thesaurus, Application Domain, Technology Topic, Popular Technical Reports.
© 2025 PatSnap. All rights reserved.Legal|Privacy policy|Modern Slavery Act Transparency Statement|Sitemap|About US| Contact US: help@patsnap.com