Aerated concrete block and preparing method thereof
A technology of aerated concrete and blocks, which is applied in the field of building materials, can solve the problems of low strength, reduce the qualified rate of finished products, increase the production cost of enterprises, etc., achieve low shrinkage value, increase tensile strength, and prevent cracks
- Summary
- Abstract
- Description
- Claims
- Application Information
AI Technical Summary
Problems solved by technology
Method used
Examples
Embodiment 1
[0028] The proportion of cement-lime-fly ash aerated concrete block is: 18 parts of lime, 12 parts of cement, 65 parts of fly ash, 4 parts of gypsum, 5 parts of waste slurry, 0.5 parts of polypropylene fiber, of which aluminum powder The dosage is obtained according to the following formula
[0029] Amount of aluminum powder per unit product (g / m 3 ) = pore volume formed after aluminum powder gassing / (theoretical gas production of aluminum at pouring temperature (l / g) * active aluminum content). The factory generally chooses on the basis of practice. In this embodiment, aluminum powder paste is used to produce aerated concrete at a rate of 600kg / m 3 As a standard, the amount of aluminum powder paste added is 8 / 10,000 of all dry materials, so the amount of aluminum powder paste added in this embodiment is 0.083 parts. The water-to-material ratio of the aerated concrete block, that is, the ratio of the total water content to the total weight of the dry material is 0.60.
[...
Embodiment 2
[0032]The proportion of cement-lime-fly ash aerated concrete block is: 20 parts of lime, 15 parts of cement, 68 parts of fly ash, 1 part of gypsum, 4 parts of waste slurry, 0.8 parts of polypropylene fiber, and aluminum powder paste The amount is 0.087 parts. The water-to-material ratio of the aerated concrete block, that is, the ratio of the total water content to the total weight of the dry material is 0.63.
[0033] The obtained aerated concrete block has a strength level of A5.0, a dry density level of B05, and a superior product (A), and a size of 600mm×200mm×250mm.
Embodiment 3
[0035] The proportion of cement-lime-fly ash aerated concrete block is: 25 parts of lime, 6 parts of cement, 70 parts of fly ash, 5 parts of gypsum, 5 parts of waste slurry, 1 part of polypropylene fiber, and adding aluminum powder paste The amount is 0.090 parts. The water-to-material ratio of the aerated concrete block, that is, the ratio of the total water content to the total weight of the dry material is 0.65.
[0036] The obtained aerated concrete block has a strength level of A5.0, a dry density level of B05, and a superior product (A), and a size of 600mm×200mm×250mm.
[0037] The method for manufacturing the air-entrained concrete block described in the above three embodiments is: according to the above ratio, add water and sand and gypsum to grind into a raw slurry, add lime, cement, waste slurry and polypropylene fiber in sequence, and stir for 2-4min Add aluminum powder and continue to stir, input steam to preheat, adjust the pouring temperature of the slurry, the...
PUM
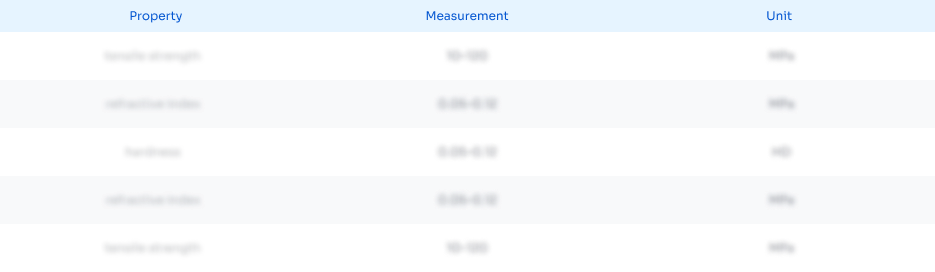
Abstract
Description
Claims
Application Information

- Generate Ideas
- Intellectual Property
- Life Sciences
- Materials
- Tech Scout
- Unparalleled Data Quality
- Higher Quality Content
- 60% Fewer Hallucinations
Browse by: Latest US Patents, China's latest patents, Technical Efficacy Thesaurus, Application Domain, Technology Topic, Popular Technical Reports.
© 2025 PatSnap. All rights reserved.Legal|Privacy policy|Modern Slavery Act Transparency Statement|Sitemap|About US| Contact US: help@patsnap.com