Tinning operation process
An operation process and tin-plating technology, applied in the direction of cells, electrolysis process, electrolysis components, etc., can solve the problems of lack of uniform standards, low production efficiency, operation errors and omissions, etc., to achieve a simple and clear operation process method, improve the effect, and improve the operation speed. Effect
- Summary
- Abstract
- Description
- Claims
- Application Information
AI Technical Summary
Problems solved by technology
Method used
Examples
Embodiment Construction
[0015] The tin plating operation process disclosed in the present invention includes the following steps: 1) Ensure that the water level and temperature of each tank are in a normal state; wear labor protection boots, acid and alkali resistant gloves or finger cots according to production requirements; ensure swing, circulation pump, DC power supply, pumping gas is in normal state;
[0016] 2) Scrub the plating tank: first add tap water to the standard liquid level of the cylinder, then add 10% sodium hydroxide solution, start the filter system and air stirring, it is best to raise the liquid temperature to 60℃, keep it for 4-8 hours, and rinse with water , And then inject the standard level of 5% sulfuric acid, the same treatment for 4-8 hours, rinse with water;
[0017] 3) Pour 1 / 4 volume of industrial pure water into the spare tank, slowly add metered sulfuric acid under stirring, add metered copper sulfate with the help of sulfuric acid to dissolve the heat released by the wate...
PUM
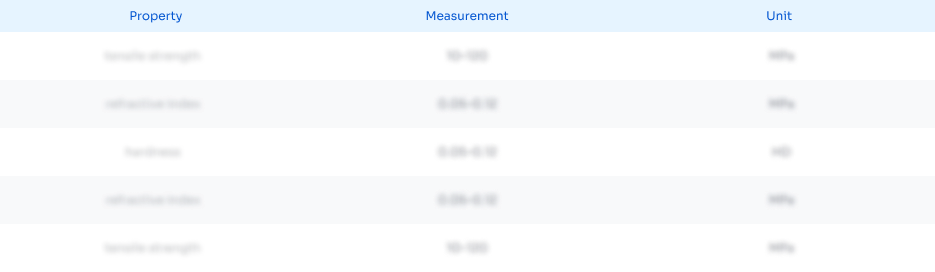
Abstract
Description
Claims
Application Information

- R&D
- Intellectual Property
- Life Sciences
- Materials
- Tech Scout
- Unparalleled Data Quality
- Higher Quality Content
- 60% Fewer Hallucinations
Browse by: Latest US Patents, China's latest patents, Technical Efficacy Thesaurus, Application Domain, Technology Topic, Popular Technical Reports.
© 2025 PatSnap. All rights reserved.Legal|Privacy policy|Modern Slavery Act Transparency Statement|Sitemap|About US| Contact US: help@patsnap.com