Steel wire surface treatment process
A surface treatment and steel wire technology, which is applied in the field of steel wire surface treatment technology, can solve the problems of low product market competitiveness, complexity, and low production efficiency, and achieve the effect of eliminating repetitive procedures, simple process, and improving work efficiency
- Summary
- Abstract
- Description
- Claims
- Application Information
AI Technical Summary
Problems solved by technology
Method used
Examples
Embodiment Construction
[0010] The technical solution disclosed in the present invention is a steel wire surface treatment process, which includes the following steps: 1) pickling: soaking in a hydrochloric acid pool for about 15 minutes at room temperature, and constantly stirring the acid pool with a steel wire during this process, so as to speed up the pickling process. The washing speed can be achieved without oxide scale;
[0011] 2) High-pressure water washing: Soak in the hydrochloric acid pool for about 15 minutes at room temperature, and continuously stir the acid pool with a steel wire during the process to speed up the pickling speed and make it free of oxide scale;
[0012] 3) Phosphating: Phosphating temperature: 50~70°C. Phosphating time: 8~15 minutes. At the same time of phosphating, attention should be paid to: close the valve in the saponification tank and open the valve in the phosphating tank. In order to improve production efficiency, the raw materials of the same batch number or...
PUM
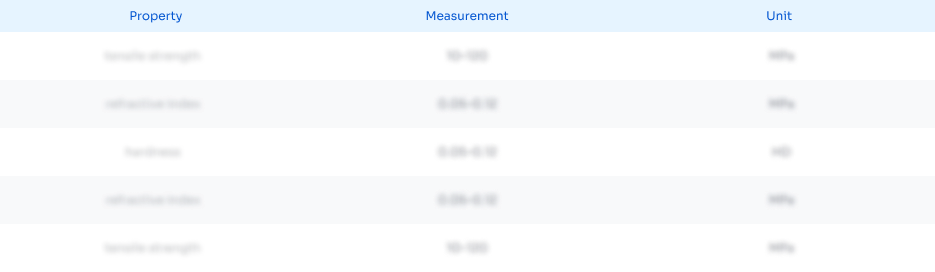
Abstract
Description
Claims
Application Information

- R&D Engineer
- R&D Manager
- IP Professional
- Industry Leading Data Capabilities
- Powerful AI technology
- Patent DNA Extraction
Browse by: Latest US Patents, China's latest patents, Technical Efficacy Thesaurus, Application Domain, Technology Topic, Popular Technical Reports.
© 2024 PatSnap. All rights reserved.Legal|Privacy policy|Modern Slavery Act Transparency Statement|Sitemap|About US| Contact US: help@patsnap.com