A low-cost converter steelmaking deoxidation process
A converter steelmaking, low-cost technology, applied in the direction of manufacturing converters, etc., can solve the problems of high cost per ton of steel, increase of non-metallic inclusions, and carbonization of molten steel, so as to reduce the content of non-metallic inclusions, reduce oxide inclusions, and improve Effect of molten steel quality
- Summary
- Abstract
- Description
- Claims
- Application Information
AI Technical Summary
Problems solved by technology
Method used
Image
Examples
Embodiment 1
[0024] For killed steel (steel grade A36Cr) process steps:
[0025] (1) Open the ladle to the tapping position of the converter, open the bottom blowing system, and the bottom blowing flow rate is 300m 3 / h;
[0026] (2) The timing starts when the steel is placed in the shaking furnace, and 0.58 kg / t of carbon powder is added after 20 seconds of tapping (the amount added per ton of steel is 0.58 kg), and the carbon powder is added within 40 seconds after tapping. In order to better achieve carbon powder deoxidation, the bottom blowing flow rate is reduced to 200m after adding carbon 3 / h, at this time, the carbon powder deoxidizes to generate CO gas to participate in the stirring of molten steel. In addition, in order to prevent the molten steel from "turning over" by adding carbon powder too early and causing safety accidents, the general tapping time is about 7 minutes, so the appropriate time to add simple carbon powder is within 20-60 seconds after tapping to ensure that...
Embodiment 2
[0032] For killed steel (steel type Q345B3) deoxidation process steps:
[0033] (1) Open the ladle to the tapping position of the converter, open the bottom blowing system, and the bottom blowing flow rate is 250m 3 / h;
[0034] (2) The timing starts when the steel is placed in the shaking furnace, and 0.36kg / t of simple carbon powder is added after 40 seconds of tapping. After adding carbon, the bottom blowing flow rate is reduced to 150m 3 / h, the simple carbon powder is added within 60S after tapping;
[0035] (3) After the carbon powder is added at an interval of 25S, add a composite deoxidizer 1.5kg / t, and all the composite deoxidizers are added within the time range of 80S to 130S after tapping; the composition (mass fraction) of the composite deoxidizer is 47.5% silicon, 24.5% calcium, 28% barium.
[0036] Specifically, in this embodiment, the simple carbon powder is added in 60 s after tapping, and all the composite deoxidizers are added in 130 s.
Embodiment 3
[0038] For killed steel (steel type Q235B2) deoxidation process steps:
[0039] (1) Open the ladle to the tapping position of the converter, open the bottom blowing system, and the bottom blowing flow rate is 200m 3 / h;
[0040] (2) The timing starts when the steel is placed in the shaking furnace, and 0.17kg / t of simple carbon powder is added after 58 seconds of tapping. After adding carbon, the bottom blowing flow rate is reduced to 100m 3 / h, the simple carbon powder is added within 60S after tapping;
[0041] (3) After the carbon powder is added at an interval of 20S, add a composite deoxidizer 1.8kg / t, and all the composite deoxidizers are added within the time range of 130S to 180S after tapping; the composition (mass fraction) of the composite deoxidizer is 44.4% silicon, 25.9% calcium, 27.7% barium and 2% aluminum.
[0042] Specifically, in this embodiment, the simple carbon powder is added in 60 s after tapping, and all the composite deoxidizers are added in 180 s...
PUM
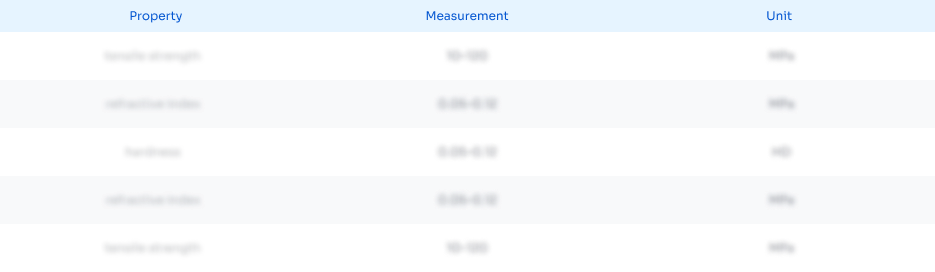
Abstract
Description
Claims
Application Information

- R&D
- Intellectual Property
- Life Sciences
- Materials
- Tech Scout
- Unparalleled Data Quality
- Higher Quality Content
- 60% Fewer Hallucinations
Browse by: Latest US Patents, China's latest patents, Technical Efficacy Thesaurus, Application Domain, Technology Topic, Popular Technical Reports.
© 2025 PatSnap. All rights reserved.Legal|Privacy policy|Modern Slavery Act Transparency Statement|Sitemap|About US| Contact US: help@patsnap.com