Calcium carbide tail gas desulfurization type depth conversion process
A technology of tail gas and calcium carbide, which is applied in the chemical industry, climate sustainability, hydrogen/synthesis gas production, etc., can solve the problems of narrow deoxidizer activation temperature zone, deactivation of deoxidizer over temperature, and high deoxidation investment, so as to reduce steam Consumption, reduced equipment investment and operating costs, and easy operation and control
- Summary
- Abstract
- Description
- Claims
- Application Information
AI Technical Summary
Problems solved by technology
Method used
Image
Examples
Embodiment Construction
[0018] figure 1 It is the flow chart of calcium carbide tail gas anaerobic deep conversion process.
[0019] This example takes the sulfur anaerobic deep conversion process for hydrogen production as an example to describe in detail: the calcium carbide tail gas (see Table 1 for the main components) after purification and pretreatment to remove trace impurities such as sulfur and arsenic is preheated by the tail gas preheater E01. After heating to 150-200°C, it is divided into three strands, accounting for 15-30%, 30-40% and 30-55% of the total gas volume respectively. After the converted product gas returned after pressurization is mixed, the dry basis concentration of CO in the mixed gas is adjusted to 30-40%, and steam is added through 1# steam mixer SP01 to adjust the water-gas ratio to 0.5-0.7, and then the mixed gas is passed through 1# Tail gas preheater E02 is further heated to 300-330°C, and sent to 1# shift furnace R01 for shift reaction;
[0020] After passing thr...
PUM
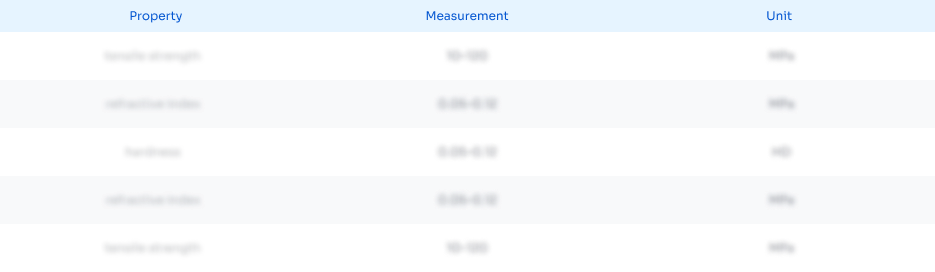
Abstract
Description
Claims
Application Information

- R&D
- Intellectual Property
- Life Sciences
- Materials
- Tech Scout
- Unparalleled Data Quality
- Higher Quality Content
- 60% Fewer Hallucinations
Browse by: Latest US Patents, China's latest patents, Technical Efficacy Thesaurus, Application Domain, Technology Topic, Popular Technical Reports.
© 2025 PatSnap. All rights reserved.Legal|Privacy policy|Modern Slavery Act Transparency Statement|Sitemap|About US| Contact US: help@patsnap.com