A double-sided cooling multifunctional high-efficiency vacuum quick-setting furnace
A double-sided cooling and multi-functional technology, applied in the field of vacuum quick-setting furnace, can solve the problems of unsatisfactory crystallization effect on the free side, large size of metal flakes, and decreased material yield, so as to improve the crystallization effect and reduce the subsequent process , The effect of stable product performance
- Summary
- Abstract
- Description
- Claims
- Application Information
AI Technical Summary
Problems solved by technology
Method used
Image
Examples
Embodiment Construction
[0012] The present invention will be further described below in conjunction with the accompanying drawings.
[0013] The double-sided cooling multi-functional high-efficiency vacuum quick-setting furnace of the present invention melts and casts pure metal raw materials in the melting chamber 1 in the inductor 2, and the metal liquid passes through the metal quick-setting and crushing mechanism 3 to quick-set and break into The small flakes then pass through the upper guiding device 4, the vacuum valve 5, the middle chamber 6, and the lower guiding device 8, and then fall into the water-cooled receiving barrel 9 for secondary cooling; the metal quick-setting and crushing mechanism 3 is to pass the molten metal through The funnel 12 and the tundish 13 flow to the water-cooled roller 18 that feeds circulating water, figure 1 The shown water-cooled roll 18 rotates in a clockwise direction and takes out the molten metal, and heat exchange occurs on the side where the molten metal c...
PUM
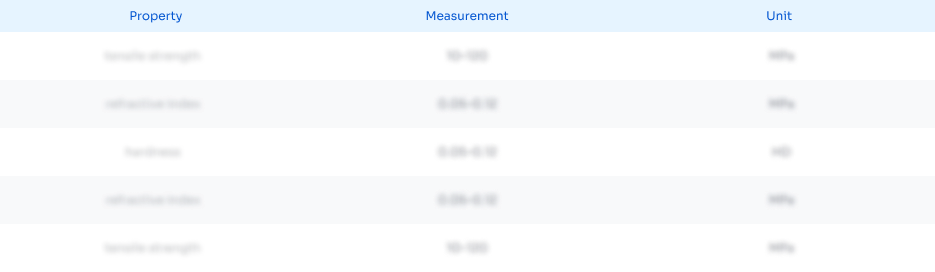
Abstract
Description
Claims
Application Information

- Generate Ideas
- Intellectual Property
- Life Sciences
- Materials
- Tech Scout
- Unparalleled Data Quality
- Higher Quality Content
- 60% Fewer Hallucinations
Browse by: Latest US Patents, China's latest patents, Technical Efficacy Thesaurus, Application Domain, Technology Topic, Popular Technical Reports.
© 2025 PatSnap. All rights reserved.Legal|Privacy policy|Modern Slavery Act Transparency Statement|Sitemap|About US| Contact US: help@patsnap.com