Mineral processing process for oolitic hematite
A technology of oolitic hematite and technology, which is applied in the direction of magnetic separation, solid separation, chemical instruments and methods, etc., can solve the problems that waste water cannot be recycled, low waste water recycling rate, long sorting process, etc., and achieve magnetization The effect is good, the cost of grinding and separation is reduced, and the recovery rate is ensured
- Summary
- Abstract
- Description
- Claims
- Application Information
AI Technical Summary
Problems solved by technology
Method used
Image
Examples
Embodiment 1
[0011] Example 1, such as figure 1 As shown, this embodiment includes the following steps: (1) crush the raw ore in a crusher to a particle size below 5mm, and roast the crushed ore in a gas-fired rotary kiln for 1 hour at a roasting temperature of 500°C. (2) Grind the roasted ore until the particle size is less than 0.074mm and the content accounts for 34%, and then use a wet magnetic separator for weak magnetic separation to magnetically separate the iron coarse concentrate 1 and tailings 1. Further preferably, the weak magnetic separation field strength of the wet magnetic separator is 120kA / m. (3) The iron coarse concentrate 1 that is magnetically separated enters the vibrating screen for screening and sorting. Entering the first magnetic separation column selection, the washing water speed of the magnetic separation column is 80ml / s. (4) The iron coarse concentrate 2 and tailings 2 are selected by the magnetic separation column; the iron coarse concentrate 2 selected by...
Embodiment 2
[0012] Example 2, such as figure 1 As shown, this embodiment includes the following steps: (1) crush the raw ore in a crusher to a particle size below 5mm, and roast the crushed ore in a gas-fired rotary kiln for at least 1 hour at a roasting temperature of 530°C. (2) Grind the roasted ore until the particle size is less than 0.074mm and the content accounts for 34%, and then use a wet magnetic separator for weak magnetic separation to magnetically separate the iron coarse concentrate 1 and tailings 1. Further preferably, the weak magnetic separation field strength of the wet magnetic separator is 120kA / m. (3) The iron coarse concentrate 1 that is magnetically separated enters the vibrating screen for screening and sorting. Entering the first magnetic separation column selection, the washing water speed of the magnetic separation column is 80ml / s. (4) Iron coarse concentrate 2 and tailings 2 are selected by the magnetic separation column; the coarse concentrate 2 selected by...
Embodiment 3
[0013] Example 3, such as figure 1 As shown, this embodiment includes the following steps: (1) crush the raw ore in a crusher to a particle size below 5mm, and roast the crushed ore in a gas-fired rotary kiln for at least 1 hour at a roasting temperature of 550°C. (2) Grind the roasted ore until the particle size is less than 0.074mm and the content accounts for 34%, and then use a wet magnetic separator for weak magnetic separation to magnetically separate the iron coarse concentrate 1 and tailings 1. The weak magnetic separation field strength of the wet magnetic separator is 120kA / m. (3) The coarse iron ore concentrate 1 that is magnetically separated enters the vibrating screen for screening. The column is selected carefully, and the washing water speed of the magnetic column is 80ml / s. (4) The iron coarse concentrate 2 and tailings 2 are selected by the magnetic separation column; the iron coarse concentrate 2 selected by the magnetic separation column is ground to a pa...
PUM
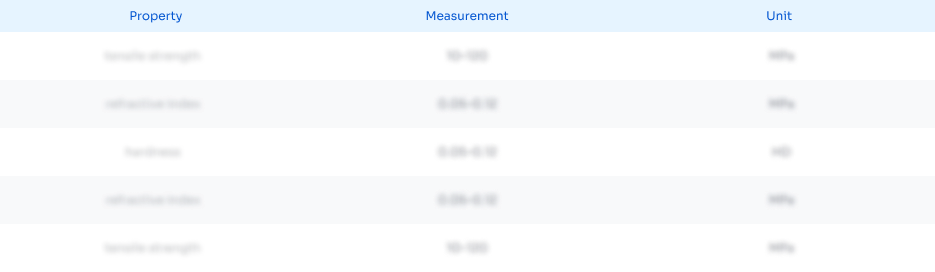
Abstract
Description
Claims
Application Information

- R&D Engineer
- R&D Manager
- IP Professional
- Industry Leading Data Capabilities
- Powerful AI technology
- Patent DNA Extraction
Browse by: Latest US Patents, China's latest patents, Technical Efficacy Thesaurus, Application Domain, Technology Topic, Popular Technical Reports.
© 2024 PatSnap. All rights reserved.Legal|Privacy policy|Modern Slavery Act Transparency Statement|Sitemap|About US| Contact US: help@patsnap.com