A blade-type composite wind energy harvester
An energy harvester and blade-type technology, applied in the direction of generators/motors, piezoelectric effect/electrostrictive or magnetostrictive motors, electrical components, etc., can solve problems such as high operating frequency, small amplitude, and complex structure , to achieve the effect of increasing the piezoelectric voltage output, increasing the frictional voltage output, and increasing the contact area
- Summary
- Abstract
- Description
- Claims
- Application Information
AI Technical Summary
Problems solved by technology
Method used
Image
Examples
Embodiment Construction
[0025] In the prior art, wind energy collectors that can achieve high output are often bulky and complex in structure. Although the existing cantilever beam structure wind energy harvester is simple in structure and small in size, its operating frequency is high and the amplitude is small, resulting in low voltage output and difficulty in obtaining ideal power output.
[0026] In view of the shortcomings of the prior art, the present invention provides a wind-powered energy harvester that can realize efficient conversion of wind energy to electric energy under the condition of low wind speed, and has the characteristics of high amplitude and high output. A blade type composite wind energy collector has two voltage output modes that cooperate with each other, a piezoelectric type and a friction type, and includes a piezoelectric energy harvesting module and a friction energy harvesting module.
[0027] The piezoelectric energy harvesting module includes blades and flexible piezoelec...
PUM
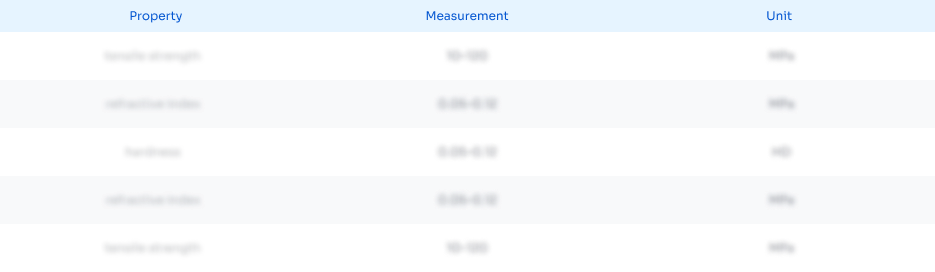
Abstract
Description
Claims
Application Information

- R&D Engineer
- R&D Manager
- IP Professional
- Industry Leading Data Capabilities
- Powerful AI technology
- Patent DNA Extraction
Browse by: Latest US Patents, China's latest patents, Technical Efficacy Thesaurus, Application Domain, Technology Topic, Popular Technical Reports.
© 2024 PatSnap. All rights reserved.Legal|Privacy policy|Modern Slavery Act Transparency Statement|Sitemap|About US| Contact US: help@patsnap.com