Vacuum glass insulation panel and preparation method thereof
A technology of vacuum glass and thermal insulation panels, which is applied in glass manufacturing equipment, glass production, glass molding, etc., and can solve the problems of poor thermal insulation performance of external walls and insulation materials that cannot be used alone for external walls.
- Summary
- Abstract
- Description
- Claims
- Application Information
AI Technical Summary
Problems solved by technology
Method used
Image
Examples
Embodiment 1
[0104] Embodiment 1: see figure 1, a low-temperature glass-sealed convex vacuum glass insulation panel. The vacuum glass insulation panel is composed of an upper convex glass 1 and a lower convex glass 2. The peripheries of the two pieces of glass are welded together by the first sealing 3 low-temperature glass solder, and the middle is a vacuum Floor. The production method is as follows: first, cut two pieces of flat glass of required size according to the shape and size of the vacuum glass insulation panel to be produced, and perform edge grinding, chamfering, cleaning and drying; secondly, put the two pieces of glass into the mold and place In the hot bending furnace, heat up to the softening temperature of the glass at 550-750°C, rely on the gravity of the glass to make the glass downward to form a convex surface, and then drop to room temperature with the furnace; again, coat the periphery of two pieces of glass or one piece of glass evenly Coat the low-temperature glass...
Embodiment 2
[0106] Example 2: see figure 1 , an adhesive-sealed convex vacuum glass insulation panel. The vacuum glass insulation panel is composed of an upper convex glass 1 and a lower convex glass 2. The periphery of the two glasses is sealed together by the first sealing 3 adhesive, and the middle is a vacuum layer. Its production method is basically the same as that of Example 1, except that the glass solder is replaced by silicone adhesive, and the sealing temperature is lowered by 100°C.
[0107] The innovative point of the present invention is that a layer of metal film is formed on the surface of the silicone adhesive by vacuum coating, thereby greatly improving the airtightness of the silicone adhesive and making the sealing of the silicone adhesive possible.
Embodiment 3
[0108] Embodiment 3: see figure 1 , a metal-sealed convex vacuum glass insulation panel, the vacuum glass insulation panel is composed of an upper convex glass 1 and a lower convex glass 2, the periphery of the two glasses is sealed together by the first sealing 3 metal tin alloy, and the middle is a vacuum Floor. The manufacturing method is basically the same as that of Example 1, except that the glass solder is replaced by tin alloy, and the sealing temperature is lowered by 160°C.
[0109] The innovation of the present invention lies in: using a tin alloy with a lower sealing temperature and vapor pressure to seal the vacuum layer can not only lower the sealing temperature, save energy and time, but also prevent a large amount of volatilization and loss of metal solder and pollute the edge sealing furnace and vacuum pump.
PUM
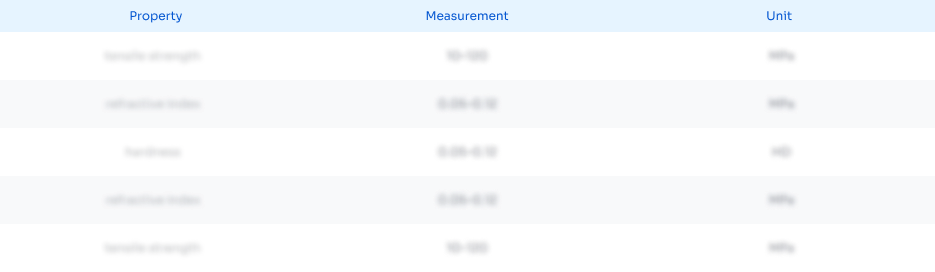
Abstract
Description
Claims
Application Information

- R&D
- Intellectual Property
- Life Sciences
- Materials
- Tech Scout
- Unparalleled Data Quality
- Higher Quality Content
- 60% Fewer Hallucinations
Browse by: Latest US Patents, China's latest patents, Technical Efficacy Thesaurus, Application Domain, Technology Topic, Popular Technical Reports.
© 2025 PatSnap. All rights reserved.Legal|Privacy policy|Modern Slavery Act Transparency Statement|Sitemap|About US| Contact US: help@patsnap.com