Synthesis of carbon material-polyimide composite film
A polyimide and composite film technology, applied in the field of composite film synthesis, can solve the problems of static charge accumulation, unsatisfactory antistatic effect, burning, explosion, etc.
- Summary
- Abstract
- Description
- Claims
- Application Information
AI Technical Summary
Problems solved by technology
Method used
Image
Examples
Embodiment 1
[0020] Example 1 Add 25ml of DMAC to a 100ml round bottom flask, add 0.8% graphene, then add 1% and acidified carbon nanotubes respectively, sonicate until there are no obvious particles, add 2.00g ODA, stir for 10min, and then divide it several times within 1h Slowly add 2.22g of PMDA, and mechanically stir for 5.5h to obtain a polyamic acid (PAA) solution whose color gradually darkens. Cast a film on a clean glass plate, place the film in an oven at 80, 100, 120, and 150°C to form the film, and soak it in distilled water. The film was fixed on a stainless steel iron frame, and placed in a muffle furnace for temperature programming, 100, 150, 200, 250, and 300°C for 1 hour each. Cool naturally to room temperature to obtain a polyimide / carbon material composite film.
[0021] figure 2 The effect of 0.8% graphene and 1% acidified carbon nanotubes on the surface resistivity of polyimide films. The figure shows that the filling of 0.8% graphene and 1% acidified carbon nanotub...
Embodiment 2
[0022] Example 2 A polyimide-carbon composite film was prepared by ultrasonic dispersion-in-situ polymerization. Add 25ml DMAC in a 100ml round bottom flask, add 0.8% graphene (at this ratio, the comprehensive performance of a single composite film is the best), then add 2% acidified carbon nanotubes respectively, sonicate until there are no obvious particles, add 2.00gODA , stirred for 10 min, then slowly added 2.22 g PMDA in 1 h several times, and mechanically stirred for 5.5 h to obtain a polyamic acid (PAA) solution with gradually darker color. Cast a film on a clean glass plate, place the film in an oven at 80, 100, 120, and 150°C to form the film, and soak it in distilled water. The film was fixed on a stainless steel iron frame, and placed in a muffle furnace for temperature programming, 100, 150, 200, 250, and 300°C for 1 hour each. Cool naturally to room temperature to obtain a polyimide / carbon material composite film.
[0023] image 3 The effect of 0.8% graphene ...
Embodiment 3
[0024] Example 3 A polyimide-carbon composite film was prepared by ultrasonic dispersion-in-situ polymerization. Add 25ml DMAC in a 100ml round bottom flask, add 0.8% graphene (at this ratio, the comprehensive performance of a single composite film is the best), then add 3% acidified carbon nanotubes respectively, sonicate until there are no obvious particles, add 2.00gODA , stirred for 10 min, then slowly added 2.22 g PMDA in 1 h several times, and mechanically stirred for 5.5 h to obtain a polyamic acid (PAA) solution with gradually darker color. Cast a film on a clean glass plate, place the film in an oven at 80, 100, 120, and 150°C to form the film, and soak it in distilled water. The film was fixed on a stainless steel iron frame, and placed in a muffle furnace for temperature programming, 100, 150, 200, 250, and 300°C for 1 hour each. Cool naturally to room temperature to obtain a polyimide / carbon material composite film.
[0025] Figure 4 The effect of 0.8% graphene...
PUM
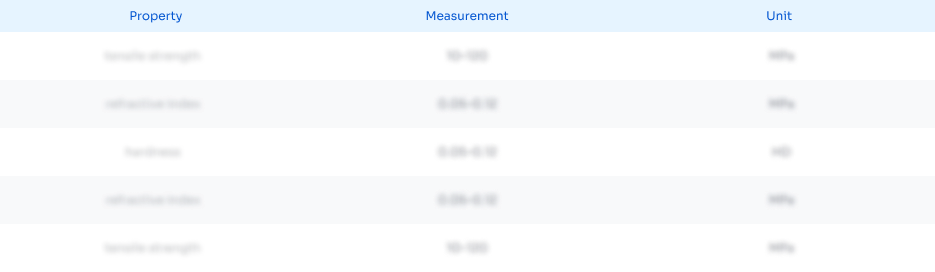
Abstract
Description
Claims
Application Information

- R&D
- Intellectual Property
- Life Sciences
- Materials
- Tech Scout
- Unparalleled Data Quality
- Higher Quality Content
- 60% Fewer Hallucinations
Browse by: Latest US Patents, China's latest patents, Technical Efficacy Thesaurus, Application Domain, Technology Topic, Popular Technical Reports.
© 2025 PatSnap. All rights reserved.Legal|Privacy policy|Modern Slavery Act Transparency Statement|Sitemap|About US| Contact US: help@patsnap.com