A papermaking wet end slurry system
A slurry and wet end technology, applied in the field of papermaking, can solve the problems of difficult water circulation operation of the wet end system, unable to meet the overall needs of the operation, and unable to peel off smoothly in sequence, and achieve guaranteed strength, good dryness and wet tensile strength. , the effect of increasing strength
- Summary
- Abstract
- Description
- Claims
- Application Information
AI Technical Summary
Problems solved by technology
Method used
Image
Examples
Embodiment approach 1
[0040] Two pulping lines are adopted to provide hardwood bleached chemical pulp (LBKP1, LBKP2) respectively, wherein LBKP1 is the first pulping line in the present invention, and the end of the LBKP2 pulping line is directly connected to the mixed stock tank, and the stock ratio is 70% LBKP1, 30% LBKP2, the refining concentration is 6% for LBKP1 and 6% for LBKP2, the refining power is 140kwh / t for LBKP1, and 80kwh / t for LBKP2, the anionic polymer is anionic guar gum, and the addition amount is 1 Kg per ton of the first fiber slurry is added in the form of an anionic guar gum solution with a concentration of 1% after brewing. After adding anionic guar gum, the first fiber slurry is modified by a refiner under high temperature and high pressure , the recorded slurry filtrate PCD is-100μeq / L; Cationic polymer is selected cationic starch, and the addition is 10 kilograms of every ton of second fiber slurry, and it is added in the form of a 4% cationic starch solution after cooking,...
Embodiment approach 2
[0042]Two pulping lines are adopted to provide hardwood bleached chemical pulp (LBKP1, LBKP2) respectively, wherein LBKP1 is the first pulping line in the present invention, and the end of the LBKP2 pulping line is directly connected to the mixed stock tank, and the stock ratio is 70% LBKP1, 30% LBKP2, the refining concentration is 6% for LBKP1 and 6% for LBKP2, the refining power is 140kwh / t for LBKP1, and 80kwh / t for LBKP2, the anionic polymer is anionic polyacrylamide, and the addition amount is 0.1 Kg per ton of the first fiber slurry, added in the form of an anionic polyacrylamide solution with a concentration of 0.2% after brewing, after adding anionic polyacrylamide, the first fiber slurry is modified by a refiner under high temperature and high pressure , the PCD of the slurry filtrate is -200μeq / L; the cationic polymer is a cationic acrylamide copolymer, and the addition amount is 1 kg per ton of the second fiber slurry, and the cationic acrylamide copolymer with a con...
PUM
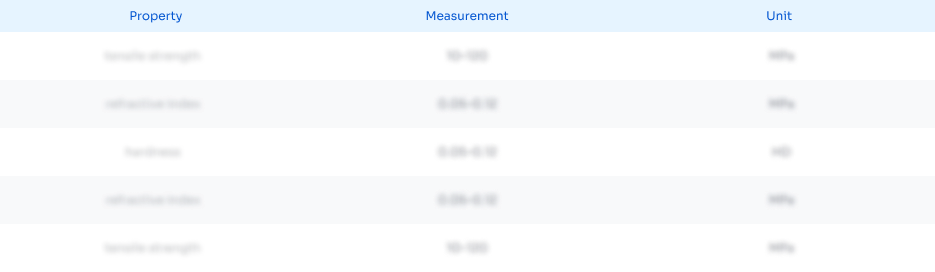
Abstract
Description
Claims
Application Information

- R&D
- Intellectual Property
- Life Sciences
- Materials
- Tech Scout
- Unparalleled Data Quality
- Higher Quality Content
- 60% Fewer Hallucinations
Browse by: Latest US Patents, China's latest patents, Technical Efficacy Thesaurus, Application Domain, Technology Topic, Popular Technical Reports.
© 2025 PatSnap. All rights reserved.Legal|Privacy policy|Modern Slavery Act Transparency Statement|Sitemap|About US| Contact US: help@patsnap.com