Marine concrete based on combined functional type additive
A technology of marine concrete and admixture, applied in the field of concrete, can solve problems such as durability decline, freeze-thaw damage, concrete structure corrosion damage, etc., and achieve the effects of improving durability performance, enhancing diffusion coefficient, and improving compressive strength
- Summary
- Abstract
- Description
- Claims
- Application Information
AI Technical Summary
Problems solved by technology
Method used
Image
Examples
Embodiment 1
[0043] This embodiment provides marine concrete based on composite functional admixture, the raw material ratio of the marine concrete is as follows:
[0044] 100 parts of hot cement, 26 parts of grade I fly ash, 27 parts of granulated blast furnace slag powder, 0.6 parts of anti-cracking and anti-corrosion plasticizer, 260 parts of medium coarse sand, 380 parts of secondary crushed stone, and 55 parts of water. The preparation method of the marine concrete is the same as that of conventional concrete, so it will not be repeated here.
[0045] By weight percentage, the anti-crack and anti-corrosion plasticizer includes the following components:
[0046] 20-30% shrinkage plasticizer, 5-15% acid and acid-generating substances, 1-6% resist, 0.1-1% catalyst, 1-3% neutralizer, 0.1- 0.3% water-repellent agent, 5-40% micro-expansion agent, 0.05-0.5% air-entraining agent, 1-5% compacting agent and 15-55% carrier. The preparation method of anti-cracking and anti-corrosion plasticizer...
Embodiment 2
[0059] In this embodiment, the raw material ratio of marine concrete is as follows:
[0060] 90 parts of hot cement, 28 parts of grade I fly ash, 26 parts of granulated blast furnace slag powder, 1 part of anti-crack and anti-corrosion plasticizer, 270 parts of medium coarse sand, 400 parts of secondary crushed stone, 60 parts of water.
[0061]Taking the preparation of 1000kg marine concrete as an example, the values (rounded) of each raw material are as follows:
[0062] 104kg of hot cement, 32kg of grade I fly ash, 30kg of granulated blast furnace slag powder, 1kg of anti-crack and anti-corrosion plasticizer, 313kg of medium and coarse sand, 452kg of grade 2 gravel, and 67kg of water.
Embodiment 3
[0064] In this embodiment, the raw material ratio of marine concrete is as follows:
[0065] 95 parts of hot cement, 30 parts of Class I fly ash, 30 parts of granulated blast furnace slag powder, 1.2 parts of anti-cracking and anti-corrosion plasticizer, 280 parts of medium coarse sand, 390 parts of secondary crushed stone, and 58 parts of water.
[0066] Taking the preparation of 1000kg marine concrete as an example, the values (rounded) of each raw material are as follows:
[0067] 107kg of hot cement, 34kg of grade I fly ash, 34kg of granulated blast furnace slag powder, 1.4kg of anti-crack and anti-corrosion plasticizer, 354kg of medium and coarse sand, 441kg of grade 2 gravel, and 66kg of water.
PUM
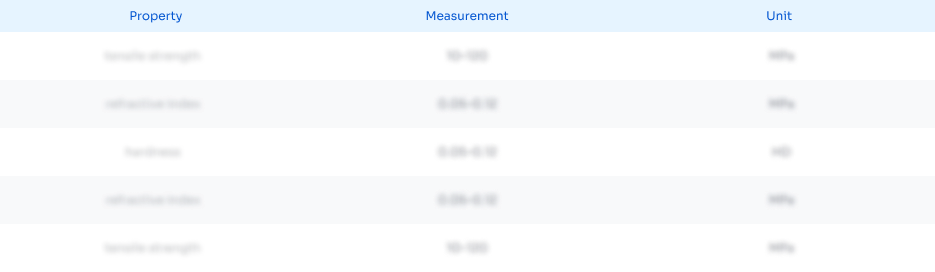
Abstract
Description
Claims
Application Information

- R&D
- Intellectual Property
- Life Sciences
- Materials
- Tech Scout
- Unparalleled Data Quality
- Higher Quality Content
- 60% Fewer Hallucinations
Browse by: Latest US Patents, China's latest patents, Technical Efficacy Thesaurus, Application Domain, Technology Topic, Popular Technical Reports.
© 2025 PatSnap. All rights reserved.Legal|Privacy policy|Modern Slavery Act Transparency Statement|Sitemap|About US| Contact US: help@patsnap.com