Method for manufacturing aluminum automobile gearbox shell
A technology of automobile gearbox and manufacturing method, which is applied in the field of metallurgy, can solve problems such as high scrap rate, unstable performance, air bubbles, etc., and achieve the effect of good bonding layer performance, performance improvement, and tight bonding
- Summary
- Abstract
- Description
- Claims
- Application Information
AI Technical Summary
Problems solved by technology
Method used
Examples
Embodiment 1
[0026] A method for manufacturing an aluminum automobile gearbox housing, which is made of an aluminum alloy consisting of the following components by weight percentage: Zn: 7%, Si: 14%, Cu: 6%, Mn : 4%, Ti: 0.8%, Re: 0.5%, Mg: 3%, Zr: 3%, Ni: 0.6%, the balance is Al and unavoidable impurities; the preparation method includes the following steps:
[0027] 1) Ingredients: According to the above ingredients, select the corresponding elemental raw material or the intermediate alloy with aluminum;
[0028] 2) Smelting: melting the raw materials prepared in step 1) at 770°C, refining and refining, and then keeping the temperature at about 740°C for pouring;
[0029] 3) Prepare the mold: preheat the mold to 240°C, and then evenly spray a layer of release agent with heat insulation and heat preservation functions in the mold cavity, and the coating thickness is 30 microns;
[0030] 4) Die-casting: The casting process parameters are: extrusion pressure 130MPa, holding time 60s, filli...
Embodiment 2
[0038] A method of manufacturing an aluminum automobile gearbox housing, which is made of an aluminum alloy consisting of the following components by weight percentage: Zn: 9%, Si: 12%, Cu: 8%, Mn : 2%, Ti: 1.2%, Re: 0.3%, Mg: 5%, Zr: 1%, Ni: 0.8%, and the balance is Al and unavoidable impurities; the preparation method includes the following steps:
[0039] 1) Ingredients: According to the above ingredients, select the corresponding elemental raw material or the intermediate alloy with aluminum;
[0040] 2) Melting: melting the raw material prepared in step 1) at 790°C, refining and refining, and then keeping the temperature at about 720°C for pouring;
[0041] 3) Prepare the mold: preheat the mold to 260°C, and then evenly spray a layer of release agent with heat insulation and heat preservation functions in the mold cavity, and the coating thickness is 25 microns;
[0042] 4) Die-casting: The casting process parameters are: extrusion pressure 150MPa, holding time 50s, fill...
Embodiment 3
[0050] A method of manufacturing an aluminum automobile gearbox housing, which is made of an aluminum alloy consisting of the following components by weight percentage: Zn: 8%, Si: 13%, Cu: 7%, Mn : 3%, Ti: 1.0%, Re: 0.4%, Mg: 4%, Zr: 2%, Ni: 0.7%, and the balance is Al and unavoidable impurities; the preparation method includes the following steps:
[0051] 1) Ingredients: According to the above ingredients, select the corresponding elemental raw material or the intermediate alloy with aluminum;
[0052] 2) Smelting: melting the raw materials prepared in step 1) at 780°C, refining and refining, and then keeping the temperature at about 730°C for pouring;
[0053] 3) Prepare the mold: preheat the mold to 250°C, and then evenly spray a layer of release agent with heat insulation and heat preservation functions in the mold cavity, and the coating thickness is 28 microns;
[0054] 4) Die casting: The casting process parameters are: extrusion pressure 140MPa, pressure holding tim...
PUM
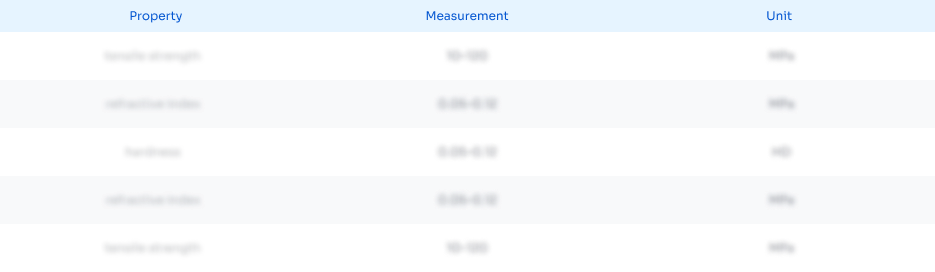
Abstract
Description
Claims
Application Information

- R&D Engineer
- R&D Manager
- IP Professional
- Industry Leading Data Capabilities
- Powerful AI technology
- Patent DNA Extraction
Browse by: Latest US Patents, China's latest patents, Technical Efficacy Thesaurus, Application Domain, Technology Topic, Popular Technical Reports.
© 2024 PatSnap. All rights reserved.Legal|Privacy policy|Modern Slavery Act Transparency Statement|Sitemap|About US| Contact US: help@patsnap.com