A Design Method of Oven Nozzle for Gravure Printing Machine
A design method and gravure printing machine technology, applied to the general parts of printing machinery, printing machines, printing, etc., can solve problems such as energy waste, achieve the effects of increasing drying time, reducing heat loss, and avoiding insufficient drying
- Summary
- Abstract
- Description
- Claims
- Application Information
AI Technical Summary
Problems solved by technology
Method used
Image
Examples
Embodiment 1
[0076] Step 1, based on the ink drying time T (0.45s) provided by the ink manufacturer, the maximum operating speed of the gravure printing machine is 200 m / min, and the minimum length of the drying box is calculated according to the following formula (1)
[0077] L=V×T=1500mm (1);
[0078] Step 2, divide the drying area of the gravure printer oven 3; divide T into t 1 (pre-drying time 1.95×10 -1 s), t 2 (Constant speed drying time 8.1×10 -2 s), t 3 (Slow drying time 1.08×10 -1 s), t 4 (compensated drying time 6.6×10 -2 s), t 1 +t 2 +t 3 +t 4 =0.449s≈0.45s, the ink drying process is divided into four drying stages: pre-drying stage, constant-speed drying stage, slow-speed drying stage and compensation drying stage, according to the four drying stages, correspondingly divide the gravure printing machine oven The four drying areas are: pre-drying area, constant-speed drying area, slow-speed drying area and compensation drying area.
[0079] Step 3, calculating the ...
Embodiment 2
[0105] Step 1, based on the ink drying time T (0.45s) provided by the ink manufacturer, the maximum operating speed of the gravure printing machine is 200 m / min, and the minimum length of the drying box is calculated according to the following formula (1)
[0106] L=V×T=1500mm (1);
[0107] Step 2, divide the drying area of the gravure machine oven 3; divide T into t 1 (pre-drying time 1.95×10 -1 s), t 2 (Constant speed drying time 8.1×10 -2 s), t 3 (Slow drying time 1.08×10 -1 s), t 4 (compensated drying time 6.6×10 -2 s), t 1 +t 2 +t 3 +t 4 =0.449s≈0.45s, the ink drying process is divided into four drying stages: pre-drying stage, constant-speed drying stage, slow-speed drying stage and compensation drying stage, according to the four drying stages, correspondingly divide the gravure printing machine oven The four drying areas are: pre-drying area, constant-speed drying area, slow-speed drying area and compensation drying area.
[0108] Step 3, calculating the ...
Embodiment 3
[0134] Step 1, based on the ink drying time T (0.45s) provided by the ink manufacturer, the maximum operating speed of the gravure printing machine is 200 m / min, and the minimum length of the drying box is calculated according to the following formula (1)
[0135] L=V×T=1500mm (1);
[0136] Step 2, divide the drying area of the gravure printer oven 3; divide T into t 1 (pre-drying time 1.95×10 -1 s), t 2 (Constant speed drying time 8.1×10 -2 s), t 3 (Slow drying time 1.08×10 -1 s), t 4 (compensated drying time 6.6×10 -2 s), t 1 +t 2 +t 3 +t 4 =0.449s≈0.45s, the ink drying process is divided into four drying stages: pre-drying stage, constant-speed drying stage, slow-speed drying stage and compensation drying stage, according to the four drying stages, correspondingly divide the gravure printing machine oven The four drying areas are: pre-drying area, constant-speed drying area, slow-speed drying area and compensation drying area.
[0137] Step 3, calculating the ...
PUM
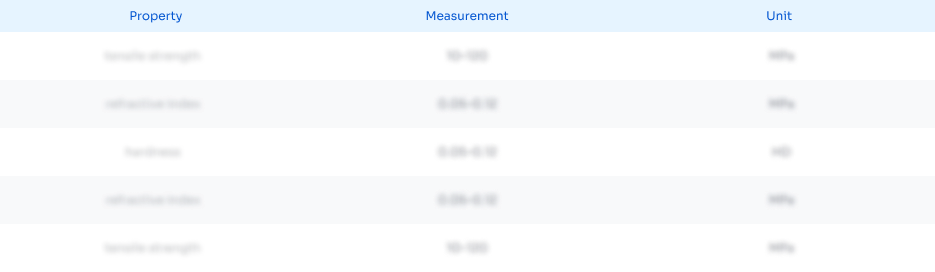
Abstract
Description
Claims
Application Information

- R&D Engineer
- R&D Manager
- IP Professional
- Industry Leading Data Capabilities
- Powerful AI technology
- Patent DNA Extraction
Browse by: Latest US Patents, China's latest patents, Technical Efficacy Thesaurus, Application Domain, Technology Topic, Popular Technical Reports.
© 2024 PatSnap. All rights reserved.Legal|Privacy policy|Modern Slavery Act Transparency Statement|Sitemap|About US| Contact US: help@patsnap.com