Rotary sewing material punching machine
A punching and sewing machine head technology, applied in the field of rotary punching machines, can solve the problems of low processing efficiency and many operation steps, and achieve the effect of improving punching efficiency
- Summary
- Abstract
- Description
- Claims
- Application Information
AI Technical Summary
Problems solved by technology
Method used
Image
Examples
Embodiment Construction
[0019] Embodiments of the present invention will be described in further detail below in conjunction with the accompanying drawings.
[0020] Figure 1 to Figure 3 Shown is the structural representation of the present invention.
[0021] Wherein the reference numerals are: sewing machine head 1, first mounting plate 11, guide sleeve mounting plate 12, guide sleeve 13, motor mounting plate 14, driven wheel 2, spline shaft sleeve 2a, driven wheel bracket 21, connecting plate 21a , mounting ring 21b, first bearing 22, spline transmission shaft 3, step surface 3a, step shaft 3b, punching knife 4, punching knife mounting seat 41, mounting groove 41a, punching knife bottom die 42, stamping cylinder 5, the second Mounting plate 51, cylinder mounting seat 52, piston rod 53, motor 6, power output shaft 61, active synchronous wheel 62, synchronous belt 63, transmission bushing 7, cavity 7a, plane bearing 71, fixing piece 72, presser foot installation Seat 8, first shaft sleeve 8a, sec...
PUM
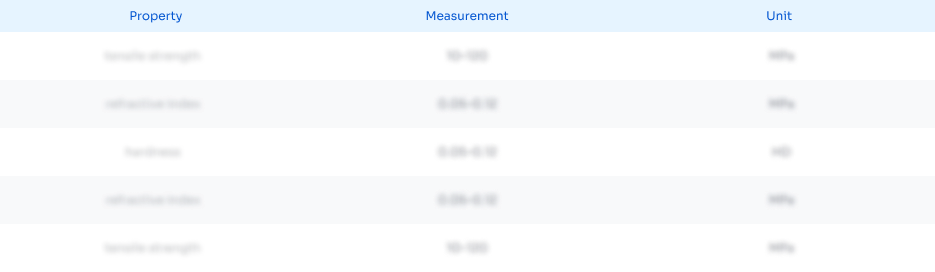
Abstract
Description
Claims
Application Information

- R&D
- Intellectual Property
- Life Sciences
- Materials
- Tech Scout
- Unparalleled Data Quality
- Higher Quality Content
- 60% Fewer Hallucinations
Browse by: Latest US Patents, China's latest patents, Technical Efficacy Thesaurus, Application Domain, Technology Topic, Popular Technical Reports.
© 2025 PatSnap. All rights reserved.Legal|Privacy policy|Modern Slavery Act Transparency Statement|Sitemap|About US| Contact US: help@patsnap.com