A method of manufacturing a torsion beam
A technology for torsion beams and pipe fittings, applied in the field of torsion beam manufacturing, can solve problems such as insufficient torsional stiffness in stamping forming, and achieve the effects of easy forming and high tensile strength
- Summary
- Abstract
- Description
- Claims
- Application Information
AI Technical Summary
Problems solved by technology
Method used
Image
Examples
Embodiment Construction
[0027] A method for preparing a torsion beam, comprising the steps of:
[0028] (1) Bending, bending the pipe to the required angle;
[0029] (2) Preforming, flattening both ends of the bent pipe fitting, and pressing the middle part of the bent pipe fitting into a V shape;
[0030] (3) Hydroforming: filling stage: put the preformed pipe into the lower mold, close the upper mold, fill with liquid, remove gas, and seal the punches at both ends of the pipe;
[0031] Forming stage: the liquid in the tube is pressurized and bulged, the punches at both ends are pushed forward to replenish the material, and the tube is basically close to the mold;
[0032] Shaping stage: increase the internal pressure to 150MPa, so that the pipe is completely attached to the mold.
[0033] The chemical composition of the pipe fittings is shown in Table 1 below in terms of weight fraction (the balance is Fe):
[0034] Table 1
[0035]
[0036]
[0037] According to the GB228-87 standard, th...
PUM
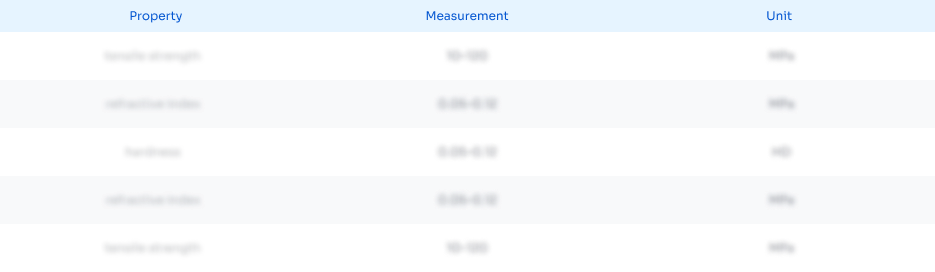
Abstract
Description
Claims
Application Information

- R&D
- Intellectual Property
- Life Sciences
- Materials
- Tech Scout
- Unparalleled Data Quality
- Higher Quality Content
- 60% Fewer Hallucinations
Browse by: Latest US Patents, China's latest patents, Technical Efficacy Thesaurus, Application Domain, Technology Topic, Popular Technical Reports.
© 2025 PatSnap. All rights reserved.Legal|Privacy policy|Modern Slavery Act Transparency Statement|Sitemap|About US| Contact US: help@patsnap.com