Hydrocarbon steam conversion catalyst and preparation method thereof
A catalyst and steam technology, applied in the field of hydrocarbon steam reforming catalyst and its preparation, can solve the problem of high preparation cost and achieve the effects of good mechanical strength, high activity and good physical and chemical properties
- Summary
- Abstract
- Description
- Claims
- Application Information
AI Technical Summary
Problems solved by technology
Method used
Image
Examples
Embodiment 1
[0034]Weigh 150g of aluminum nitrate, 14.3g of zirconium nitrate, 7.1g of nickel nitrate, and 23.2g of magnesium nitrate, dissolve them in 425ml of water and stir for 10min to obtain solution 1. Weigh 113.6 g of potassium carbonate and dissolve it in 610 ml of water to obtain solution 2. Solution 1 and Solution 2 were co-currently mixed uniformly in a 25kHz ultrasonic oscillator at a constant temperature of 25°C, and 27.6g of metakaolin, 9.2g of calcium hydroxide, and 6.5g of potassium hydroxide were added and shaken for 30 minutes to obtain mixed solution 3. Naturally cool to room temperature, take it out, wash, and dry at 80°C for 48 hours to obtain a solid semi-finished product. Mix the semi-finished product with 0.90g of graphite and ball mill, add an appropriate amount of water, knead and extrude, and heat up to 480°C at a rate of 2.5°C / min after drying , Calcined at constant temperature for 2h, then raised to 950°C for 2.5h at a rate of 2°C / min to obtain Catalyst A. The...
Embodiment 2
[0036] Weigh 150g of aluminum nitrate, 42.2g of zirconium nitrate, 10.4g of nickel nitrate, and 1.32g of magnesium nitrate, dissolve them in 472ml of water and stir for 10min to obtain solution 1. Weigh 113g of potassium carbonate and dissolve it in 610ml of water to obtain solution 2. Solution 1 and solution 2 were mixed uniformly in a 30kHz ultrasonic oscillator at a constant temperature of 50°C in parallel, and 20.3g of metakaolin, 5.4g of calcium hydroxide, and 3.4g of potassium hydroxide were added and shaken for 35 minutes to obtain mixed solution 3. Naturally cool to room temperature, take it out, wash, and dry at 100°C for 24 hours to obtain a solid semi-finished product. Mix the semi-finished product with 1.0g of graphite and ball mill, add an appropriate amount of water, knead and extrude, and heat up to 450°C at a rate of 2°C / min after drying , roasted at a constant temperature for 2 hours, and then raised to 850 °C for 2.5 hours at a rate of 2 °C / min to obtain cata...
Embodiment 3
[0038] Weigh 75g of aluminum nitrate, 21.5g of zirconium nitrate, 5.1g of nickel nitrate, and 0.56g of potassium nitrate, dissolve them in 275ml of water and stir for 10min to obtain solution 1. Weigh 43.5 g of sodium carbonate and dissolve it in 410 ml of water to obtain solution 2. Solution 1 and solution 2 were mixed uniformly in a 40kHz ultrasonic oscillator at a constant temperature of 75°C in parallel, and 47.9g of metakaolin, 7.5g of calcium hydroxide, and 3.7g of potassium hydroxide were added and shaken for 45min to obtain mixed solution 3. Naturally cool to room temperature, take it out, wash, and dry at 90°C for 36 hours to obtain a solid semi-finished product. After mixing the semi-finished product with 1.1g of graphite and ball milling, add an appropriate amount of water for kneading and extrusion molding. After drying, heat up to 450°C at a rate of 2°C / min. , calcination at constant temperature for 2 hours, and then calcination at 950 ℃ at a rate of 2 ℃ / min for 2...
PUM
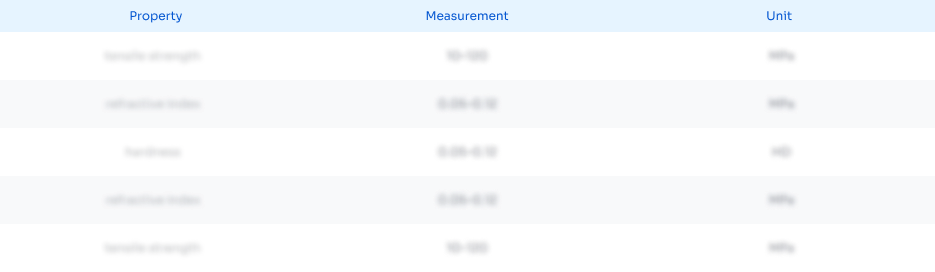
Abstract
Description
Claims
Application Information

- R&D Engineer
- R&D Manager
- IP Professional
- Industry Leading Data Capabilities
- Powerful AI technology
- Patent DNA Extraction
Browse by: Latest US Patents, China's latest patents, Technical Efficacy Thesaurus, Application Domain, Technology Topic, Popular Technical Reports.
© 2024 PatSnap. All rights reserved.Legal|Privacy policy|Modern Slavery Act Transparency Statement|Sitemap|About US| Contact US: help@patsnap.com