High-performance carbon fiber reinforced polyamide composite material and preparation method thereof
A composite material and carbon fiber technology, applied in the field of carbon fiber reinforced polyamide composite materials, can solve the problems of surface structure damage, carbon fiber mechanical performance reduction, poor compatibility, etc., achieve high mechanical performance retention rate, improve compatibility, compatibility sex increasing effect
- Summary
- Abstract
- Description
- Claims
- Application Information
AI Technical Summary
Problems solved by technology
Method used
Image
Examples
Embodiment 1
[0038] Place 0.3g of chopped carbon fiber in 110°C, 0.05mol / L Michaelis acid / ethylbenzene solution, react for 2h, wash with absolute ethanol several times after the reaction, and dry in a vacuum environment at 80°C for 6h to obtain Carbon fibers with surface carboxyl functionalization;
[0039] Weigh 2.52kg of polyamide resin, dry at 100°C for 4h, weigh 0.15kg of toughening agent, 7.5g of antioxidants 1010 and 168, and 15g of lubricant and mix them uniformly in a high-speed mixer to obtain a resin mixture;
[0040] Add the homogeneously mixed resin mixture into the twin-screw extruder (the diameter of the screw is 35mm, and the ratio of length to diameter is L / D=36) through the main feed port, and the carbon fiber after surface carboxyl functionalization treatment is added through the side feed port To the extruder, the control temperature of each section of the twin-screw extruder (from the feeding port to the nozzle outlet) is 220°C, 230°C, 235°C, 235°C, 235°C, 235°C, 235°C,...
Embodiment 2
[0043] Place 0.6g of chopped carbon fiber in a 0.05mol / L Michaelis acid / ethylbenzene solution at 110°C, react for 2h, wash with absolute ethanol several times after the reaction, and dry in a vacuum environment at 80°C for 6h to obtain Carbon fibers with surface carboxyl functionalization;
[0044] Weigh 2.22 kg of polyamide resin, dry at 100°C for 4 hours, weigh 0.15 kg of toughening agent, 7.5 g of antioxidants 1010 and 168, and 15 g of lubricant and mix them uniformly in a high-speed mixer to obtain a resin mixture;
[0045]Add the homogeneously mixed resin mixture into the twin-screw extruder (the diameter of the screw is 35mm, and the ratio of length to diameter is L / D=36) through the main feed port, and the carbon fiber after surface carboxyl functionalization treatment is added through the side feed port To the extruder, the control temperature of each section of the twin-screw extruder (from the feeding port to the nozzle outlet) is 220°C, 230°C, 235°C, 235°C, 235°C, 2...
Embodiment 3
[0048] Place 0.6g of chopped carbon fiber in a 0.05mol / L Michaelis acid / ethylbenzene solution at 110°C, react for 1h, wash with absolute ethanol several times after the reaction, and dry in a vacuum environment at 80°C for 6h to obtain Carbon fibers with surface carboxyl functionalization;
[0049] Weigh 2.22 kg of polyamide resin, dry at 100°C for 4 hours, weigh 0.15 kg of toughening agent, 7.5 g of antioxidants 1010 and 168, and 15 g of lubricant and mix them uniformly in a high-speed mixer to obtain a resin mixture;
[0050] Add the homogeneously mixed resin mixture into the twin-screw extruder (the diameter of the screw is 35mm, and the ratio of length to diameter is L / D=36) through the main feed port, and the carbon fiber after surface carboxyl functionalization treatment is added through the side feed port To the extruder, the control temperature of each section of the twin-screw extruder (from the feeding port to the nozzle outlet) is 220°C, 230°C, 235°C, 235°C, 235°C, ...
PUM
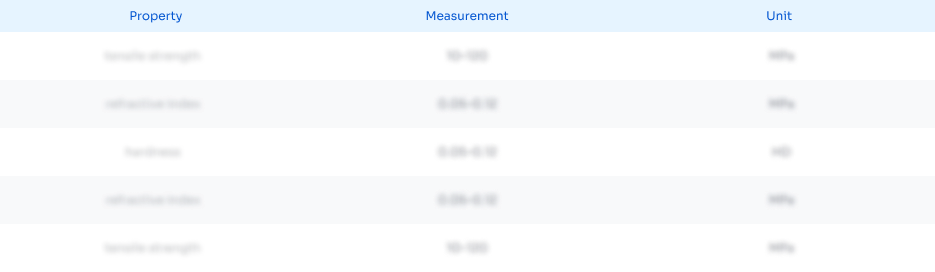
Abstract
Description
Claims
Application Information

- R&D Engineer
- R&D Manager
- IP Professional
- Industry Leading Data Capabilities
- Powerful AI technology
- Patent DNA Extraction
Browse by: Latest US Patents, China's latest patents, Technical Efficacy Thesaurus, Application Domain, Technology Topic, Popular Technical Reports.
© 2024 PatSnap. All rights reserved.Legal|Privacy policy|Modern Slavery Act Transparency Statement|Sitemap|About US| Contact US: help@patsnap.com