Method for preparing paraffin hydrocarbon shape-selective isomerization catalyst
A catalyst and isomerization technology, which is applied in the field of preparation of paraffin hydrocarbon type-selective isomerization catalysts, can solve the problems of low activity and selectivity, weak catalyst acidity, and easy cracking
- Summary
- Abstract
- Description
- Claims
- Application Information
AI Technical Summary
Problems solved by technology
Method used
Image
Examples
Embodiment 1
[0027] (1) Dissolve chloroplatinic acid containing 0.3 grams of platinum in 6 grams of water, fully mix 10 grams of 200-mesh cellulose with the above solution, and dry the mixture at 80°C for 6 hours to obtain platinum-loaded cellulose.
[0028] (2) 45 grams of ZSM-22, 72 grams of aluminum hydroxide dry rubber powder (SB produced by Condean, Germany, 76% on a dry basis), the platinum-loaded cellulose prepared in step (1), and 50 ml of cellulose with a concentration of 0.2M The nitric acid solution and 30ml of water are fully mixed and kneaded to make it into a paste-like plastic, and a cylindrical strip with a diameter of 1.5mm is formed on an extruder, and the cylindrical strip is dried at 110°C for 8 hours, and then roasted at 650°C for 4 hours in an air atmosphere Get a catalyst. The pore volume of the catalyst with a pore diameter of 1-10nm accounts for 7.4% of the total pore volume, and the pore volume of 100-1000nm accounts for 46.6% of the total pore volume.
Embodiment 2~8
[0030] With embodiment 1, difference is that the kind and consumption of various substances are adjusted in each step, and the composition of catalyst is different, and each embodiment catalyst number is respectively E-2~E-8, and evaluation condition is the same as embodiment 1, The pore-forming dosage and catalyst composition used in the catalysts of each embodiment are shown in Table 2, and the evaluation results are shown in Table 3.
Embodiment 9
[0036] E1~E8 and C1~C2 were evaluated for catalyst performance, and the evaluation conditions were as follows: take 10ml of catalyst, dilute it with 10ml of quartz sand, fill it into a fixed-bed micro-continuous reactor, and evaluate its catalytic activity. Before the evaluation, under the conditions of pressure 1MPa and temperature 200°C, pure hydrogen was introduced at a rate of 800 gas volume ratio (the volume ratio of the gas entering to the loading volume of the catalyst), and the temperature was raised to 320°C for 4 hours. Carry out catalyst activation; Then, under constant pressure and temperature, the molar ratio of hydrogen to hydrocarbon is adjusted to 4, and the volume space velocity is 1.0h -1 Enter the raw materials shown in Table 1, carry out catalyst activity evaluation, get the product of reacting for 4 hours and analyze, the composition of catalyst is shown in Table 2, and the evaluation results are shown in Table 3.
[0037] Table 2 The amount of pore formin...
PUM
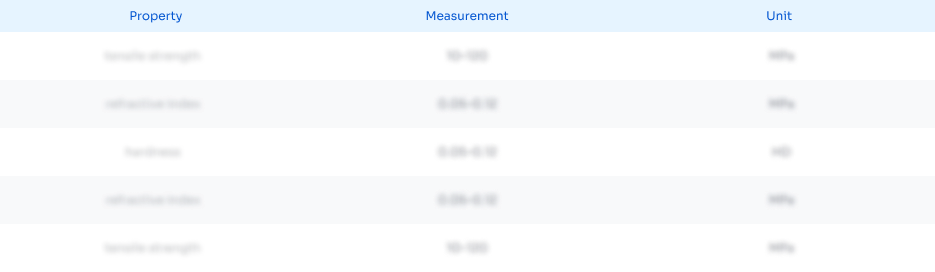
Abstract
Description
Claims
Application Information

- R&D
- Intellectual Property
- Life Sciences
- Materials
- Tech Scout
- Unparalleled Data Quality
- Higher Quality Content
- 60% Fewer Hallucinations
Browse by: Latest US Patents, China's latest patents, Technical Efficacy Thesaurus, Application Domain, Technology Topic, Popular Technical Reports.
© 2025 PatSnap. All rights reserved.Legal|Privacy policy|Modern Slavery Act Transparency Statement|Sitemap|About US| Contact US: help@patsnap.com