Profile-assisted standing and pre-embedded integrally formed 3D hollow composite floor and manufacturing method
A technology for assisting standing and composite floors, which is applied to building structures, floors, buildings, etc., can solve problems such as low production efficiency, high cost, and poor compressive strength, and achieve low equipment investment, strong designability, and avoid layered effect
- Summary
- Abstract
- Description
- Claims
- Application Information
AI Technical Summary
Problems solved by technology
Method used
Image
Examples
Embodiment 1
[0054] This embodiment provides a profile assisted standing and pre-embedded integrally formed 3D hollow composite floor and its manufacturing method; the profile assisted standing and pre-embedded integrally formed 3D hollow composite floor includes a brushed structure 3D hollow composite floor that constitutes the overall frame of the 3D hollow composite floor The fabric, the two warp profiles arranged in the napped region of the brushed structure 3D hollow fabric, and the two weft profiles arranged in the voids of the napped warp structure layer of the brushed structure 3D hollow fabric.
[0055] The formation of the pile warp area in the brushed structure 3D hollow fabric is to remove the pile warp yarns during the weaving process of the 3D hollow fabric so that it does not participate in the weaving of the fabric, thus forming a space area without the pile warp core column as The velvet brushed area; the velvet brushed area is located at the edge of the 3D hollow fabric. ...
Embodiment 2
[0085] This embodiment provides a profile assisted standing and pre-embedded integrally formed 3D hollow composite floor and its manufacturing method; the profile assisted standing and pre-embedded integrally formed 3D hollow composite floor includes a brushed structure 3D hollow composite floor that constitutes the overall frame of the 3D hollow composite floor The fabric, the two warp profiles arranged in the napped region of the brushed structure 3D hollow fabric, and the two weft profiles arranged in the voids of the napped warp structure layer of the brushed structure 3D hollow fabric.
[0086] The formation of the pile warp area in the brushed structure 3D hollow fabric is to remove the pile warp yarns during the weaving process of the 3D hollow fabric so that it does not participate in the weaving of the fabric, thus forming a space area without the pile warp core column as The velvet brushed area; the velvet brushed area is located at the edge of the 3D hollow fabric. ...
PUM
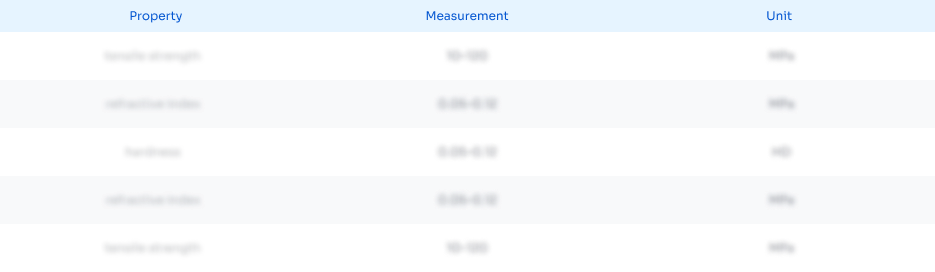
Abstract
Description
Claims
Application Information

- Generate Ideas
- Intellectual Property
- Life Sciences
- Materials
- Tech Scout
- Unparalleled Data Quality
- Higher Quality Content
- 60% Fewer Hallucinations
Browse by: Latest US Patents, China's latest patents, Technical Efficacy Thesaurus, Application Domain, Technology Topic, Popular Technical Reports.
© 2025 PatSnap. All rights reserved.Legal|Privacy policy|Modern Slavery Act Transparency Statement|Sitemap|About US| Contact US: help@patsnap.com