A method and application for real-time monitoring of biogas fermentation system
A technology of real-time monitoring and biogas fermentation, applied in biochemical equipment and methods, measurement/inspection of microorganisms, introduction of foreign genetic material using carriers, etc., can solve problems such as high cost, long detection cycle, and inability to accurately reflect cell biomass , to achieve the effect of accurate monitoring and optimization of gas production
- Summary
- Abstract
- Description
- Claims
- Application Information
AI Technical Summary
Problems solved by technology
Method used
Image
Examples
Embodiment 1
[0033] Example 1: Correlation between Clostridium cellulolyticum cell growth density and fluorescence density
[0034] Clostridium cellulolyticum was purchased from German Culture Collection (DSM5812). The gfp gene was amplified using the plasmid pMUTIN-gfp as a template.
[0035] The upstream primer is F: 5'-CG GGATCC AAGAAGATATACATATGGCT-3' (SEQ ID NO. 1);
[0036] The downstream primer is R: 5'-CG GGATCC CTCGAATTCATTATTTGTAG-3' (SEQ ID NO.2), the underline is the restriction site of BamH I.
[0037] The amplification system was 25 μL, and the reaction program was as follows: template pre-denaturation at 95°C for 5 minutes; denaturation at 95°C for 30 seconds, annealing at 52°C for 30 seconds, and extension at 72°C for 90 seconds. A total of 30 cycles, with a final extension at 72°C for 10 min. PCR amplified products were separated by 1% agarose gel electrophoresis and purified using a purification kit. The PCR product and the pET15b vector were respectively digested...
Embodiment 2
[0040] Example 2: Monitoring the activity of GFP-labeled Clostridium cellulolyticum (DAM5812-GFP) in a leaky reactor
[0041] Corn stalks were crushed into 1×1cm block material, mixed with activated sludge according to the VS ratio of 2:1, then an appropriate amount of water was added to adjust the total TS content to 8%, and NH4Cl was added to supplement the nitrogen source, and NaHCO 3 Adjust the alkalinity to 3000mg CaCO 3 / L. Use 2M NaOH solution to absorb H 2 S, CO 2 Such as acid gas, the gas production is measured by the lye discharge method, which is the methane production. Cultivate DSM5812-GPF under anaerobic conditions until OD 600 When the growth reached 0.45, the cells were collected by centrifugation, and the cells were resuspended with a small amount of medium. Under the protection of N2, the bacterial solution was added to the seepage anaerobic reactor. Bacteria are evenly distributed by the seepage fluid circulation method. At 0, 2, 5, 10, and 15 days of...
Embodiment 3
[0043] Example 3 Effect of raw material pretreatment on hydrolyzing microorganisms in biogas fermentation flora
[0044] The corn stalks were crushed into a 1×1 cm block, and water was added to adjust the TS to 10%. Add 6% NaOH (w / w), at 30°C, 100 rpm, for 3d. After the end, the solid-liquid separation is carried out by pressing to obtain the alkali-treated straw. Alkali-treated straw and untreated straw were used as fermentation substrates, mixed with activated anaerobic sludge at a VS ratio of 2:1, and fermented in a seepage reactor. Fermentation conditions, strain addition and sampling determination are the same as those described in Example 2.
[0045] The results showed that the concentration of DSM5812-GFP detected in the initial alkaline treatment reactor was lower, indicating that the straw surface was more susceptible to microbial adsorption after pretreatment. As the fermentation progressed, alkali treatment of straw destroyed the physical barrier effect of lignin...
PUM
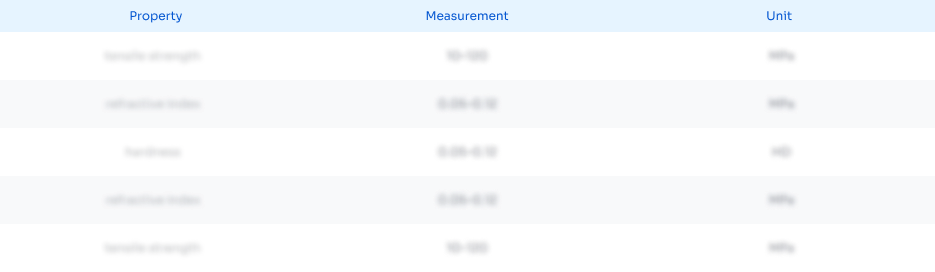
Abstract
Description
Claims
Application Information

- R&D Engineer
- R&D Manager
- IP Professional
- Industry Leading Data Capabilities
- Powerful AI technology
- Patent DNA Extraction
Browse by: Latest US Patents, China's latest patents, Technical Efficacy Thesaurus, Application Domain, Technology Topic, Popular Technical Reports.
© 2024 PatSnap. All rights reserved.Legal|Privacy policy|Modern Slavery Act Transparency Statement|Sitemap|About US| Contact US: help@patsnap.com