Composite fabric dyeing and finishing process
A kind of cloth, craft technology
- Summary
- Abstract
- Description
- Claims
- Application Information
AI Technical Summary
Problems solved by technology
Method used
Examples
Embodiment 1
[0020] A dyeing and finishing process for composite fabrics, comprising the steps of:
[0021] 1) Pretreatment;
[0022] 2) dyeing;
[0023] 3) Finishing: Put 1-2 parts by weight of gum arabic powder, 0.9 parts by weight of fatty alcohol polyoxyethylene ether sodium sulfate, 1.1 parts by weight of lavender essence, and 1.4 parts by weight of olive oil polyethylene glycol ester into 24 parts by weight in turn. In deionized water, stir evenly; then simultaneously drop 0.7 parts by weight of camphor powder, 0.9 parts by weight of zinc hydroxystannate, 1.2 parts by weight of zinc acetate, and 2.3 parts by weight of triethanolamine ester quaternary ammonium salt, continue to stir until fully mixed, and obtain Finishing solution; then pad the fabric in the finishing solution, take it out and dry it at a constant temperature.
Embodiment 2
[0025] The dyeing and finishing process of composite fabrics includes the following steps:
[0026] 1) Pretreatment;
[0027] 2) dyeing;
[0028] 3) Finishing: Put 1 weight part of gum arabic powder, 0.9 weight part of fatty alcohol polyoxyethylene ether sodium sulfate, 1.1 weight part of lavender essence, and 1.4 weight part of olive oil polyethylene glycol ester into 24 parts by weight of deionized water in sequence , stir evenly; then drop into 0.7 parts by weight of camphor powder, 0.9 parts by weight of zinc hydroxystannate, 1.2 parts by weight of zinc acetate, 2.3 parts by weight of triethanolamine ester quaternary ammonium salt, and continue to stir until fully mixed and uniform to obtain a finishing solution ; Then pad the fabric in the finishing solution, take it out and dry it at a constant temperature.
Embodiment 3
[0030] The dyeing and finishing process of composite fabrics includes the following steps:
[0031] 1) pretreatment;
[0032] 2) dyeing;
[0033] 3) Finishing: Put 2 parts by weight of gum arabic powder, 0.9 parts by weight of fatty alcohol polyoxyethylene ether sodium sulfate, 1.1 parts by weight of lavender essence, and 1.4 parts by weight of olive oil polyethylene glycol ester into 24 parts by weight of deionized water in sequence , stir evenly; then drop into 0.7 parts by weight of camphor powder, 0.9 parts by weight of zinc hydroxystannate, 1.2 parts by weight of zinc acetate, 2.3 parts by weight of triethanolamine ester quaternary ammonium salt, and continue to stir until fully mixed and uniform to obtain a finishing solution ; Then pad the fabric in the finishing solution, take it out and dry it at a constant temperature.
PUM
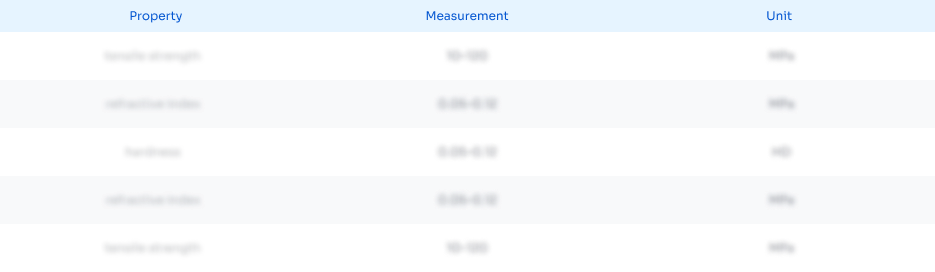
Abstract
Description
Claims
Application Information

- R&D Engineer
- R&D Manager
- IP Professional
- Industry Leading Data Capabilities
- Powerful AI technology
- Patent DNA Extraction
Browse by: Latest US Patents, China's latest patents, Technical Efficacy Thesaurus, Application Domain, Technology Topic, Popular Technical Reports.
© 2024 PatSnap. All rights reserved.Legal|Privacy policy|Modern Slavery Act Transparency Statement|Sitemap|About US| Contact US: help@patsnap.com