Hydraulic system for recycling elastic potential energy generated by deformation of test pieces
An elastic potential energy, hydraulic system technology, applied in the direction of fluid pressure actuating system components, fluid pressure actuating devices, servo motors, etc., can solve the problems of high cost, large driving force, high vibration frequency, and reduce test costs and work. High efficiency and the effect of energy recovery and utilization
- Summary
- Abstract
- Description
- Claims
- Application Information
AI Technical Summary
Problems solved by technology
Method used
Image
Examples
Embodiment Construction
[0028] The principles and features of the present invention are described below in conjunction with the accompanying drawings, and the examples given are only used to explain the present invention, and are not intended to limit the scope of the present invention.
[0029] like figure 1 As shown, a hydraulic system that recycles the deformation elastic potential energy of the test piece, the first accumulator 1, the first reversing valve 2, the hydraulic cylinder 3, the second reversing valve 4, the second accumulator 5, the hydraulic motor 6 and the first hydraulic pump 7, the first accumulator 1, the first reversing valve 2 and the hydraulic cylinder 3 are connected through the oil pipe in sequence, the hydraulic cylinder 3, the second reversing valve 4, the second accumulator 5. The hydraulic motor 6 and the first hydraulic pump 7 are sequentially connected through the oil pipe, and the first hydraulic pump 7 is connected with the first accumulator 1 through the oil pipe.
...
PUM
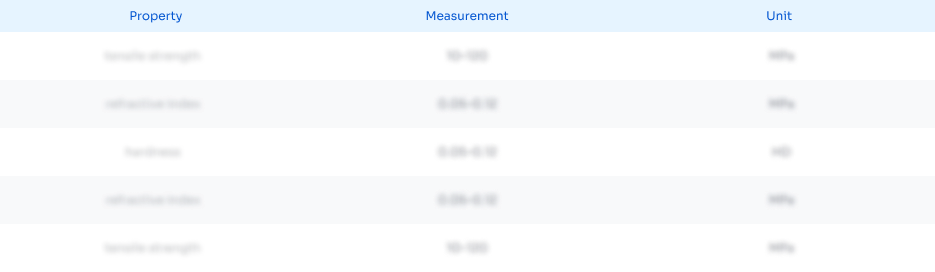
Abstract
Description
Claims
Application Information

- Generate Ideas
- Intellectual Property
- Life Sciences
- Materials
- Tech Scout
- Unparalleled Data Quality
- Higher Quality Content
- 60% Fewer Hallucinations
Browse by: Latest US Patents, China's latest patents, Technical Efficacy Thesaurus, Application Domain, Technology Topic, Popular Technical Reports.
© 2025 PatSnap. All rights reserved.Legal|Privacy policy|Modern Slavery Act Transparency Statement|Sitemap|About US| Contact US: help@patsnap.com