Comprehensive treatment method for mixed waste residues
A technology for comprehensive treatment and mixing of waste residues, applied in the direction of improving process efficiency, etc., can solve problems such as limited reference significance, waste of resources, poor adaptability, etc., and achieve high comprehensive recovery rate, simple process, and strong adaptability of raw materials Effect
- Summary
- Abstract
- Description
- Claims
- Application Information
AI Technical Summary
Problems solved by technology
Method used
Image
Examples
Embodiment 1
[0029] a kind of like figure 1 The comprehensive treatment method of the mixed waste slag shown in the present invention comprises the following steps:
[0030] (1) Mix the anode slime decopper slag, lead matte slag, lead-containing waste slag, pulverized coal slag, and waste CRT glass at a mass ratio of 5:1:1:10:20, and add reducing agent coke (accounting for mixing The mass fraction of waste slag is 5%) for high-temperature smelting at 1300° C. for about 4 hours to obtain a large amount of secondary smelting slag, a small amount of crude iron-copper alloy and lead-zinc fumes. The soot and iron-copper alloy are returned to other smelting projects for recycling, and the composition of the secondary smelting slag is: SiO 2 40%, Al 2 o 3 25%, CaO2.5%, K 2 O+Na 2 O23.2%, MgO8%, Fe 2 o 3 0.5%, ZnO0.2% and Sn0.6%.
[0031] (2) the secondary smelting slag that step (1) obtains and lead-free CRT glass, quartz sand, additive (the mixture of calcite, aluminum feldspar, barium c...
Embodiment 2
[0034] a kind of like figure 1 The comprehensive treatment method of the mixed waste slag shown in the present invention comprises the following steps:
[0035] (1) Mix anode slime decopper slag, lead matte slag, lead-containing waste slag, pulverized coal slag, and waste CRT glass at a mass ratio of 5:2:2:20:20, and add reducing agent coke (accounting for the mixed The mass fraction of waste slag is 3%) for high-temperature smelting at a melting temperature of 1350°C and a smelting time of about 3.5 hours to obtain a large amount of secondary smelting slag, a small amount of crude iron-copper alloy and lead-zinc fumes. The soot and iron-copper alloy are returned to other smelting projects for recycling, and the composition of the secondary smelting slag is: SiO 2 36%, Al 2 o 3 25%, CaO4.9%, K 2 O+Na 2 O23%, MgO7.6%, Fe 2 o 3 1%, ZnO0.5% and Sn2%.
[0036] (2) The secondary smelting slag obtained in step (1) is prepared according to the batching ratio by secondary smel...
Embodiment 3
[0039] a kind of like figure 1 The comprehensive treatment method of the mixed waste slag shown in the present invention comprises the following steps:
[0040] (1) Mix anode slime decopper slag, lead matte slag, lead-containing waste slag, coal powder slag, and waste CRT glass at a mass ratio of 7:2:2:15:15, and add reducing agent coke (accounting for mixing The mass fraction of waste slag is 4%) for high-temperature smelting at a melting temperature of 1350° C. and a smelting time of about 4 hours to obtain a large amount of secondary smelting slag, a small amount of crude iron-copper alloy and lead-zinc fumes. The soot and iron-copper alloy are returned to other smelting projects for recycling, and the composition of the secondary smelting slag is: SiO 2 40%, Al 2 o 3 23%, CaO4.9%, K 2 O+Na 2 O25%, MgO6%, Fe 2 o 3 0.7%, ZnO0.1% and Sn0.3%.
[0041] (2) The secondary smelting slag obtained in step (1) is prepared according to the batching ratio by secondary smelting ...
PUM
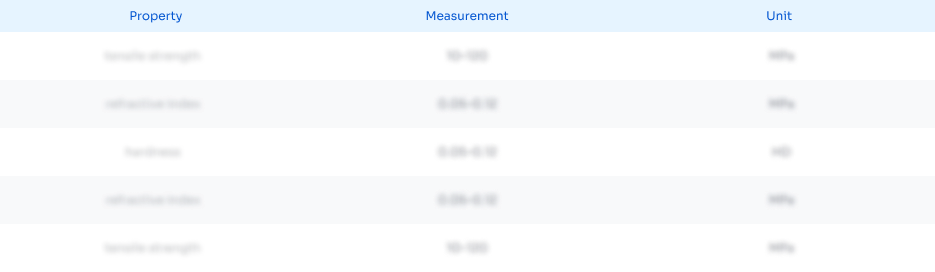
Abstract
Description
Claims
Application Information

- Generate Ideas
- Intellectual Property
- Life Sciences
- Materials
- Tech Scout
- Unparalleled Data Quality
- Higher Quality Content
- 60% Fewer Hallucinations
Browse by: Latest US Patents, China's latest patents, Technical Efficacy Thesaurus, Application Domain, Technology Topic, Popular Technical Reports.
© 2025 PatSnap. All rights reserved.Legal|Privacy policy|Modern Slavery Act Transparency Statement|Sitemap|About US| Contact US: help@patsnap.com