Torsion residual stress ultrasonic nondestructive test method
A residual stress, non-destructive testing technology, applied in the direction of measuring force, measuring device, instrument, etc.
- Summary
- Abstract
- Description
- Claims
- Application Information
AI Technical Summary
Problems solved by technology
Method used
Image
Examples
Embodiment Construction
[0011] The specific embodiment of the present invention is described in detail below:
[0012] Torsional residual stress refers to the residual internal stress of transmission components such as shafts and cylinders during processing and service, which has an important impact on the life and safety of transmission components. Here, the drive shaft is taken as an example to detect the torsional residual stress in the 30° torsional direction.
[0013] 1. Shaft torsion residual stress detection principle
[0014] According to the theory of acoustoelasticity, when ultrasonic waves propagate in isotropic elastic media, when the polarization direction of wave particles is consistent with or opposite to the direction of residual stress, the change of ultrasonic wave velocity is linearly related to the change of residual stress. Therefore, the torsional residual stress of the shaft can be detected by ultrasonic critically refracted longitudinal waves.
[0015] σ ...
PUM
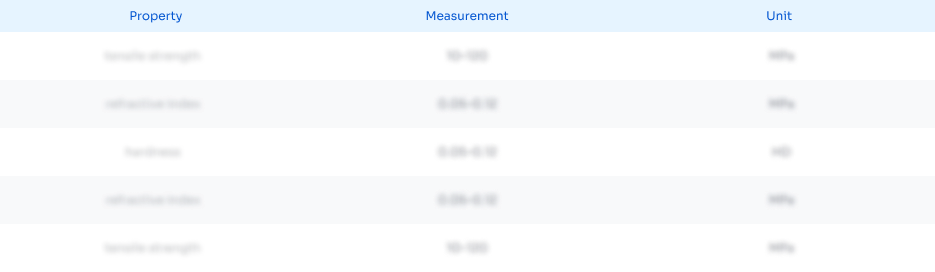
Abstract
Description
Claims
Application Information

- Generate Ideas
- Intellectual Property
- Life Sciences
- Materials
- Tech Scout
- Unparalleled Data Quality
- Higher Quality Content
- 60% Fewer Hallucinations
Browse by: Latest US Patents, China's latest patents, Technical Efficacy Thesaurus, Application Domain, Technology Topic, Popular Technical Reports.
© 2025 PatSnap. All rights reserved.Legal|Privacy policy|Modern Slavery Act Transparency Statement|Sitemap|About US| Contact US: help@patsnap.com