Floating oil seal with ceramic composite wear-resisting face and metal stamping ring bodies
A technology of metal stamping and ceramic compounding, applied in the direction of engine seals, engine components, mechanical equipment, etc., can solve the problems of high cost and low productivity, and achieve the effects of improving service life, improving wear resistance and easy processing
- Summary
- Abstract
- Description
- Claims
- Application Information
AI Technical Summary
Problems solved by technology
Method used
Image
Examples
Embodiment 1
[0045] Such as image 3 As shown, the floating oil seal with ceramic composite wear-resistant surface and metal stamping ring body in this embodiment includes a pair of sealing ring bodies 1 with symmetrical upper and lower structures. The sealing ring body 1 is formed by secondary stamping of a metal sheet. A groove 3 for arranging the sealing ring 2 is arranged on the outer side of the sealing ring body 1, and the sealing ring 2 is arranged in the groove. The working surface 4 of the sealing ring body 1 is provided with a wear-resistant belt assembly groove 5 , and a wear-resistant belt 6 is fixedly installed in the wear-resistant belt installation groove 5 . The wear-resistant band 6 is made of zirconia ceramic powder with a zirconia content of 80% and an original grain size of 5-10 μm. After dry pressing, the blank is sintered at a high temperature of 1480°C. The friction surface 7 of the wear-resistant belt 6 protrudes from the working surface 4 of the sealing ring body ...
Embodiment 2
[0048] Such as Figure 4 As shown, the floating oil seal with ceramic composite wear-resistant surface and metal stamping ring body in this embodiment includes a pair of sealing ring bodies 1 with symmetrical upper and lower structures. The sealing ring body 1 is formed by stamping three times from a thin metal plate, and the surface After phosphating treatment, a groove 3 for arranging the sealing ring 2 is arranged on the outer side of the sealing ring body 1, and the sealing ring 2 is arranged in the groove. The working surface 4 of the sealing ring body 1 is provided with a wear-resistant belt assembly groove 5 , and a wear-resistant belt 6 is fixedly installed in the wear-resistant belt installation groove 5 . The wear-resistant band 6 is made of alumina ceramic powder with an alumina content of 99% and a primary grain size of 5-10 μm, which is formed by dry pressing and sintered at a high temperature of 1580-1620°C. The friction surface 7 of the wear-resistant belt 6 is...
PUM
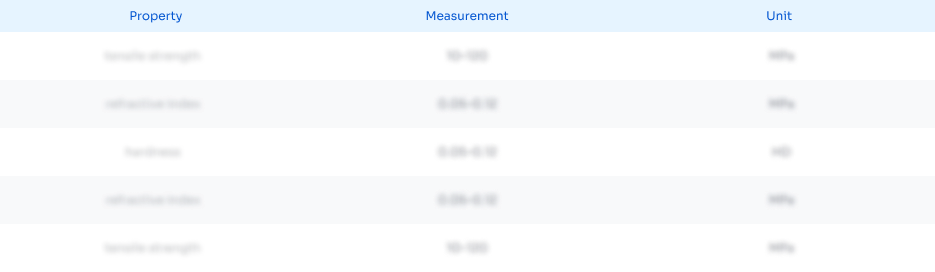
Abstract
Description
Claims
Application Information

- R&D
- Intellectual Property
- Life Sciences
- Materials
- Tech Scout
- Unparalleled Data Quality
- Higher Quality Content
- 60% Fewer Hallucinations
Browse by: Latest US Patents, China's latest patents, Technical Efficacy Thesaurus, Application Domain, Technology Topic, Popular Technical Reports.
© 2025 PatSnap. All rights reserved.Legal|Privacy policy|Modern Slavery Act Transparency Statement|Sitemap|About US| Contact US: help@patsnap.com